Baka Yoke is a Japanese term that translates to “fool-proofing.” It is a quality control technique that helps prevent mistakes and defects from occurring during the production process. By proactively identifying and addressing potential problems, it helps to ensure that the final product meets the highest quality standards.
Purpose of Baka Yoke
The purpose of Baka Yoke is to eliminate defects and minimize waste in the production process. By proactively identifying and addressing potential problems, it helps to ensure that the final product meets the desired quality standards. This helps to reduce costs, improve efficiency, and increase customer satisfaction.
Types of Baka Yoke
Physical Baka Yoke
It involves the use of physical devices to prevent defects from occurring. This may include the use of jigs, fixtures, and other mechanical devices to ensure that parts are assembled correctly.
Process Baka Yoke
This involves the design of processes and procedures to prevent defects from occurring. This may include the use of standardized work instructions, checklists, and other tools to ensure that each step in the production process is performed correctly.
Information Baka Yoke
It involves the use of technology and data to prevent defects from occurring. This may include the use of barcodes, RFID tags, and other tracking systems to ensure that the correct materials and components are used during production.
Benefits
Improved Quality
Baka Yoke helps to ensure that the final product meets the desired quality standards by proactively identifying and addressing potential problems. This results in improved product quality, which can lead to increased customer satisfaction and loyalty.
Reduced Costs
By preventing defects from occurring, it helps to reduce the cost of production by minimizing the need for rework and the amount of waste generated during the production process. This can result in significant cost savings over time.
Increased Efficiency
It helps to improve the efficiency of the production process by reducing the amount of time required to correct mistakes and perform rework. This results in faster production times, which can increase overall production capacity and output.
Better Visibility
It provides better visibility into the production process by proactively identifying and addressing potential problems. This helps to identify areas for improvement and can lead to the implementation of more efficient processes and procedures.
Implementing Baka Yoke
Assess Current Processes
The first step in implementing Baka Yoke is to assess the current production processes and identify areas where defects are most likely to occur. This may include reviewing work instructions, checklists, and other process documentation to identify potential problems.
Identify Techniques
Once the potential problem areas have been identified, the next step is to identify the appropriate Baka Yoke techniques to address these problems. This may include the use of physical devices, process improvements, or information technologies.
Implement Techniques
The next step is to implement the identified Baka Yoke techniques. This may include the design and implementation of physical devices, the development of new processes and procedures, and the implementation of new technologies.
Monitor and Evaluate Results
Once Baka Yoke techniques have been implemented, it is important to monitor and evaluate the results to ensure that the desired outcomes are being achieved. This may include tracking the number of defects, measuring the time required to perform rework, and evaluating customer satisfaction. Based on the results, adjustments can be made to these techniques to further improve the production process.
Continuously Improve
Baka Yoke is an ongoing process that requires continuous improvement. As production processes change, it is important to regularly assess the effectiveness of these techniques and identify areas for improvement.
Baka Yoke is a valuable tool for quality control that helps to ensure that the final product meets the desired quality standards. By proactively identifying and addressing potential problems, it helps to reduce costs, improve efficiency, and increase customer satisfaction. Implementing it requires a systematic approach, including the assessment of current processes, the identification of appropriate Baka Yoke techniques, the implementation of these techniques, and ongoing monitoring and evaluation.
Master Lean and Six Sigma Acronyms in No Time!
The Ultimate Guide to LSS Lingo – Yours for Free
Subscribe and Get Your Hands on the Most Comprehensive List of 220+ LSS Acronyms Available. No more searching for definitions, no more confusion. Just pure expertise at your fingertips. Get your free guide and other ebooks and templates today. Download Now!
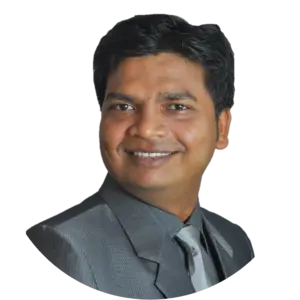
Sachin Naik
Passionate about improving processes and systems | Lean Six Sigma practitioner, trainer and coach for 14+ years consulting giant corporations and fortune 500 companies on Operational Excellence | Start-up enthusiast | Change Management and Design Thinking student | Love to ride and drive
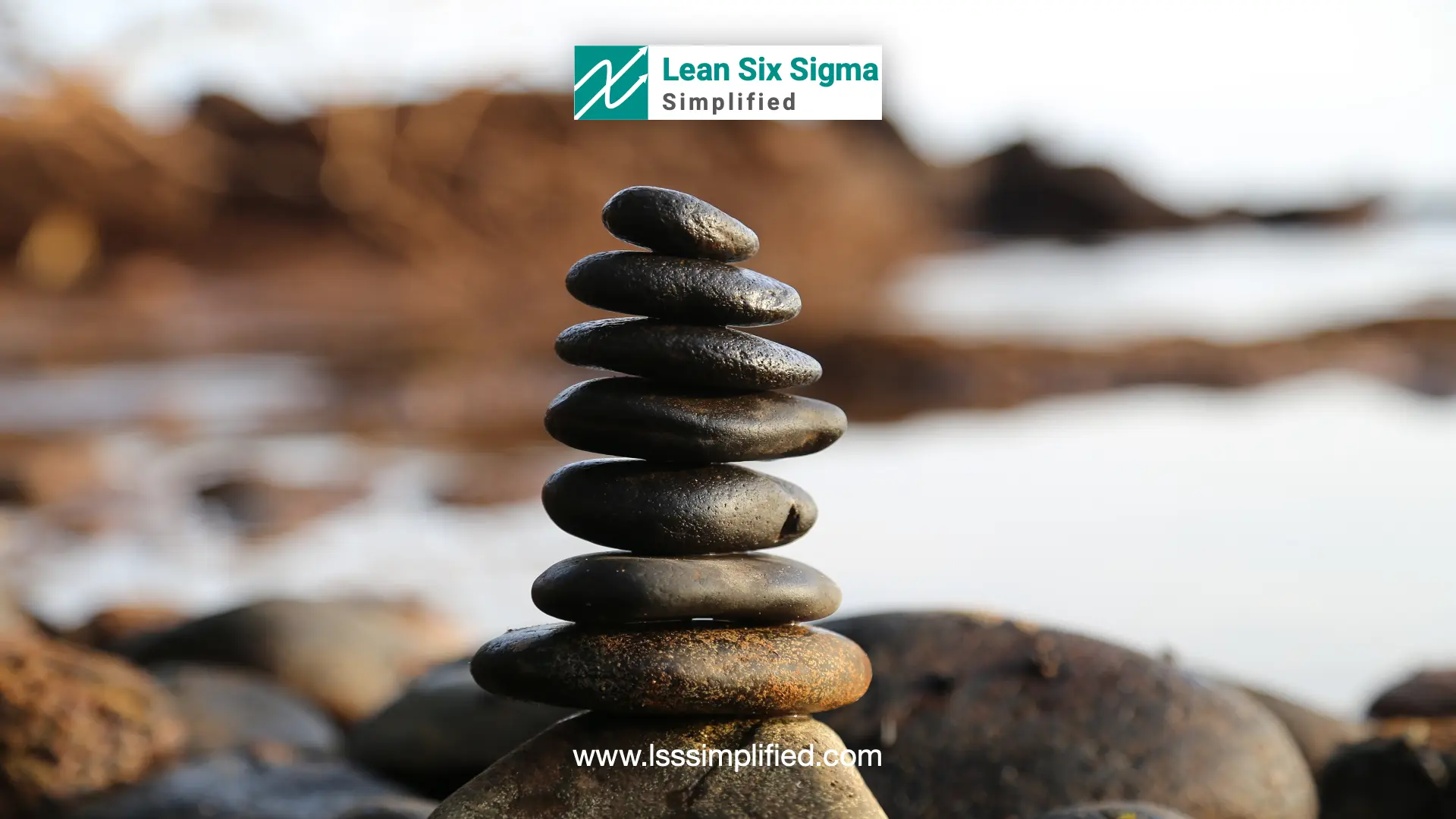
7 Principles of Lean
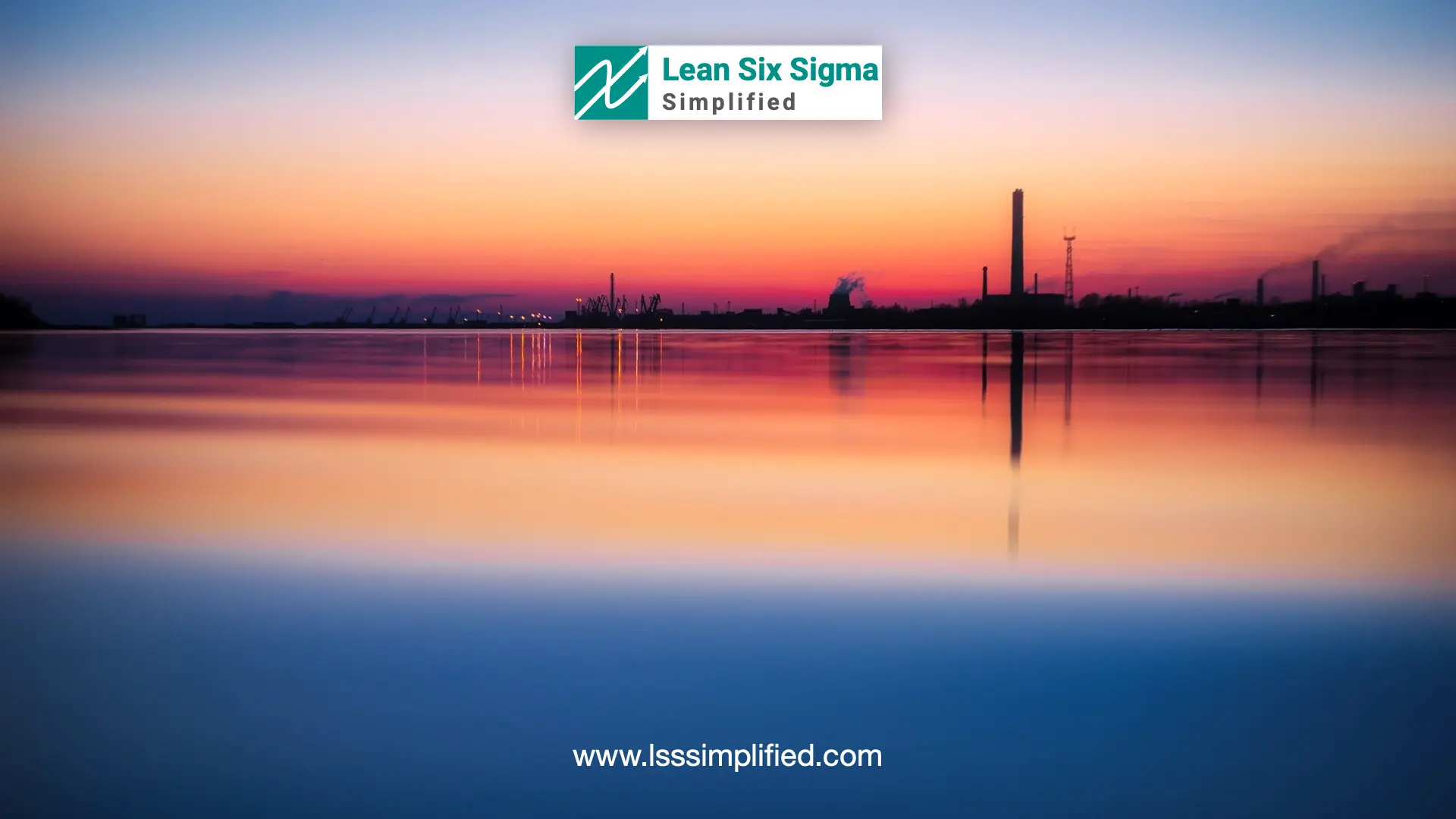
Origin of Lean

Next generation Lean Six Sigma – Harnessing the Power of AI

What is Lean Six Sigma and how it helps your career
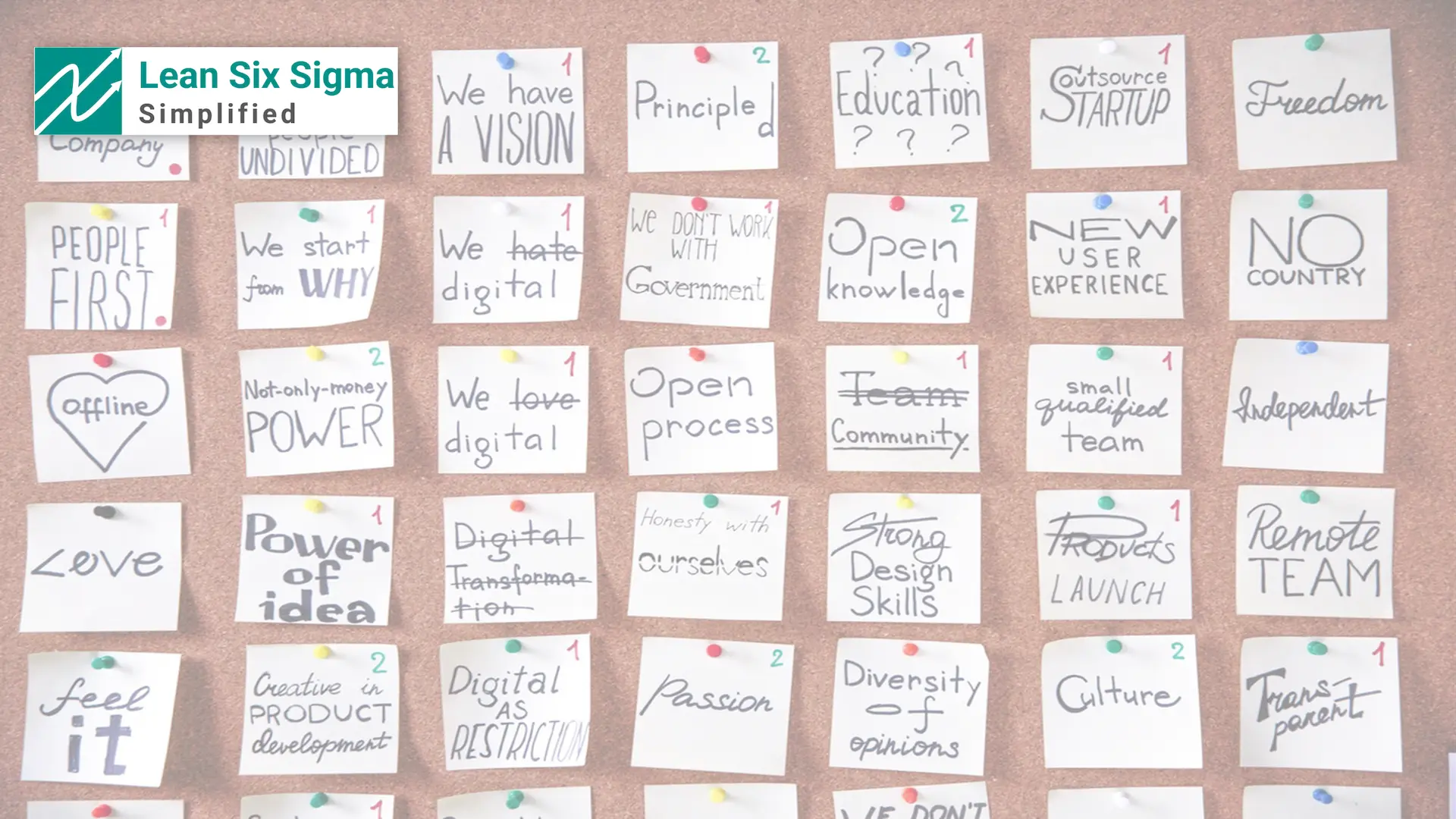
Nominal Group Technique Definition, Examples Steps
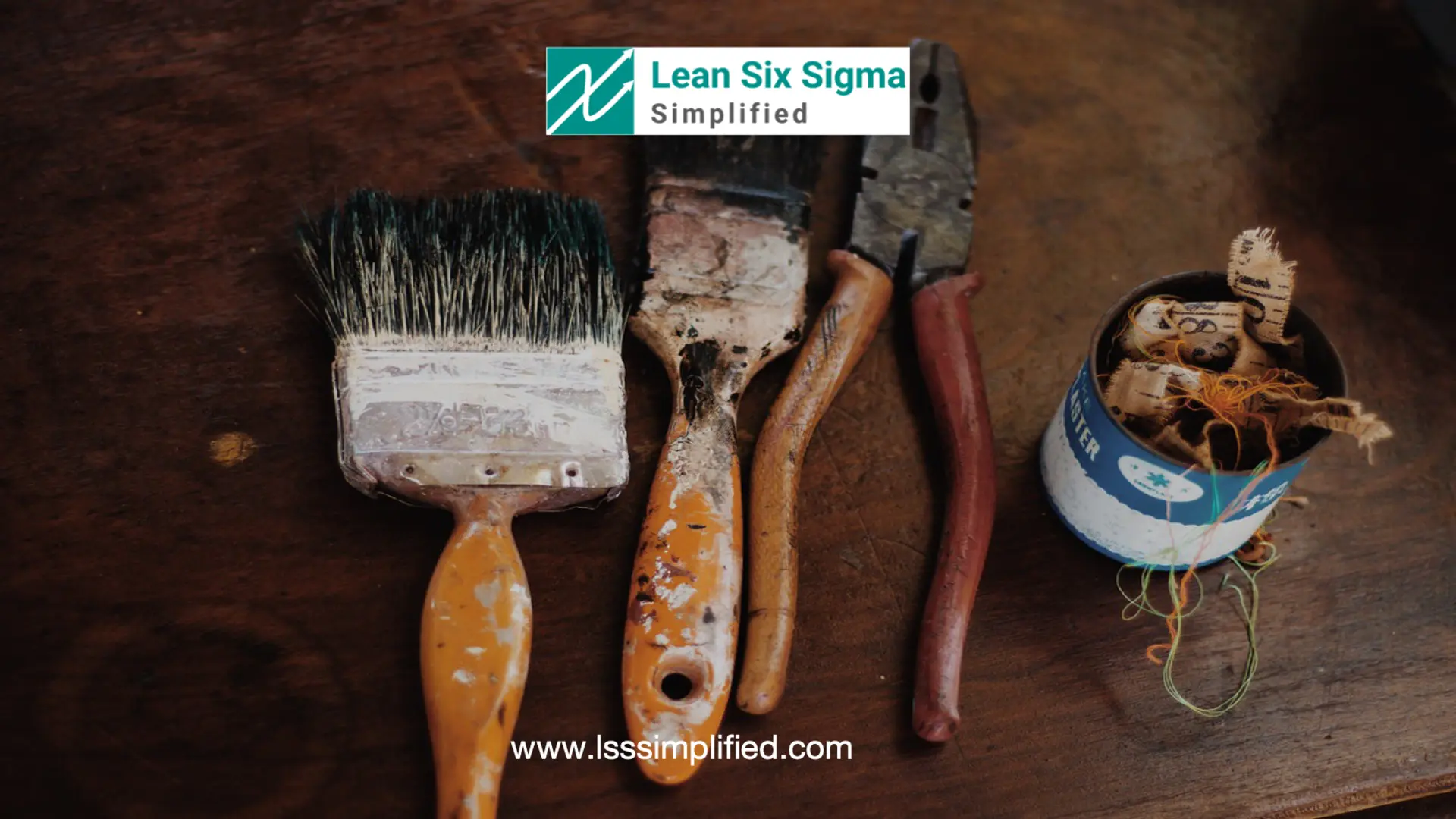
What are the measures of Variation

What are the measures of Central Tendency
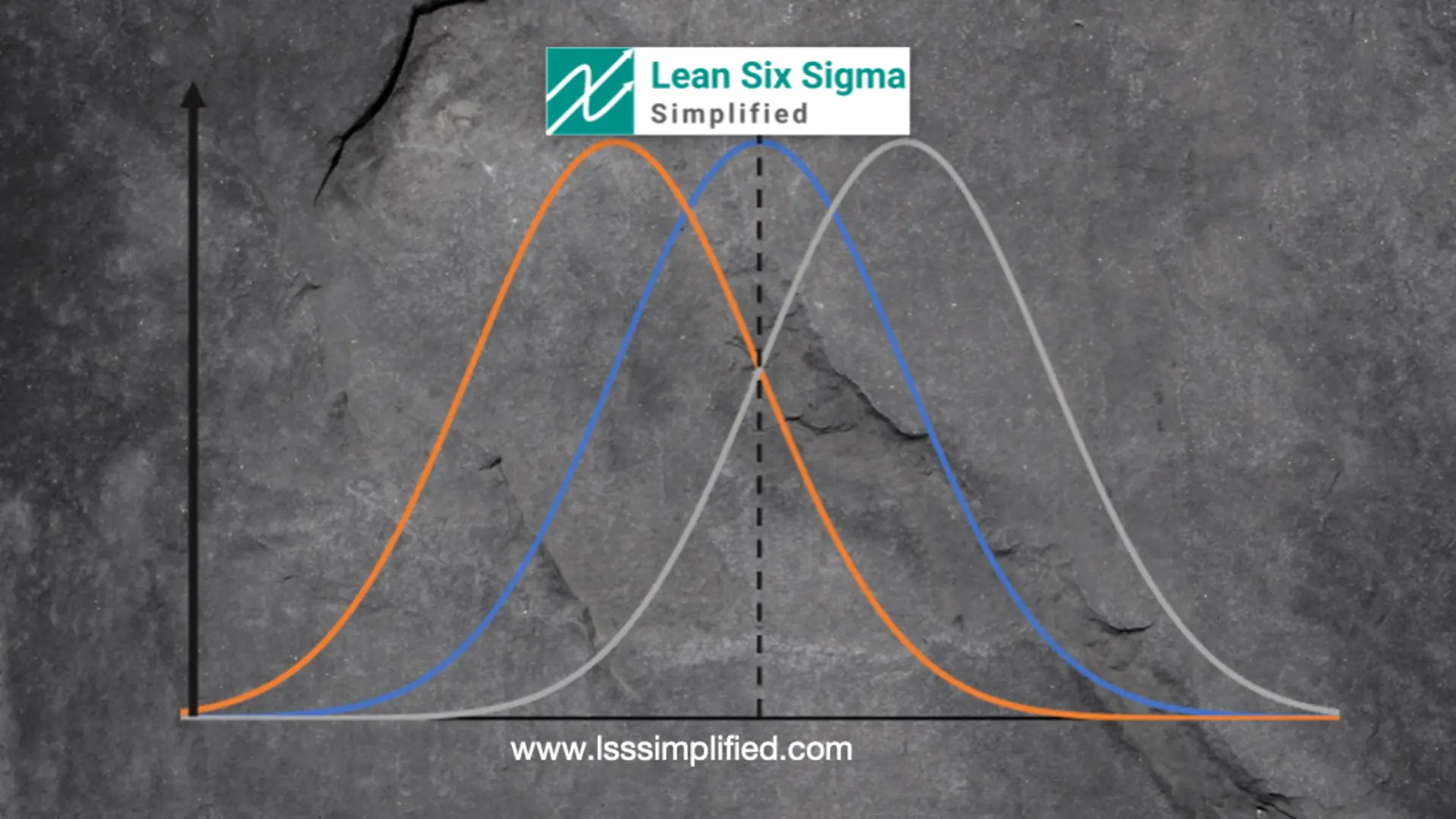
Normal Distribution for Lean Six Sigma

Probability Distribution for Lean Six Sigma
