The Lean methodology, developed by Taiichi Ohno, is built on a foundation of 7 principles of Lean that are designed to increase efficiency, reduce waste, and improve overall quality. These 7 principles of Lean form the foundation of this methodology and are essential to understanding the origins of TPS (Toyota Production System) and Lean.
In my last post, I spoke about the origin of Lean and its evolution into what it is today. Hope you went through the same. If not, please click here to read the same (opens in a new tab). It gives the background to these 7 principles of Lean and understand why these are important to know.
The 7 Principles of Lean and Toyota Production System (TPS) are listed below.
- Elimination of Waste
- Continues Improvement
- Respect for People
- Focus on Value
- Continuous Flow
- Pull system
- Strive for perfection
We will explore each of these 7 principles of lean in this post.
Please note, although these seems very similar to 5 basic principles of lean, these are not the same. 5 basic principles of lean are an evolved version of these 7 principles. Moreover, the 5 principles gives us a defined structure to follow for process improvement. The 7 principles of lean were more of design principles used to come up with Toyota Production System and Lean.

1st Principle of Lean – Elimination of Waste
Elimination of Waste is a fundamental principle of 7 principles of Lean and is aimed at improving efficiency and reducing waste in all areas of the organization. The goal is to create value for customers by streamlining processes and reducing unnecessary activities, materials, and time.
Waste can take many forms, including overproduction, waiting, unnecessary motion, excess inventory, defects, overprocessing, unused talent, and unused information. By identifying and eliminating these forms of waste, organizations can improve their overall efficiency and effectiveness.
One of the key benefits of the elimination of waste is the improvement of cycle times, which refers to the amount of time it takes to complete a process or produce a product. By streamlining processes and reducing waste, cycle times can be reduced, leading to improved responsiveness and faster delivery times.
Another important benefit of eliminating waste is the reduction of costs. By reducing waste and improving efficiency, organizations can save time, money, and resources, which can be used to invest in other areas of the business. This can also lead to improved customer satisfaction, as organizations are able to offer high-quality products and services at a lower cost.
2nd Principle of Lean – Continuous Improvement
Continuous Improvement is one of the 7 principles of Lean that emphasizes making small, incremental changes to processes, products, and services over time to achieve better results. It is an ongoing process that never ends and is driven by a desire to improve and to make things better.
One of the key elements of continuous improvement is the use of data and metrics to track progress and identify areas for improvement. By collecting and analyzing data, organizations can see where they are making progress and where they need to make changes. This information is then used to drive continuous improvement and make changes that will lead to better results.
Another key element of continuous improvement is the use of teamwork and collaboration. Teams work together to identify areas for improvement, come up with solutions, and implement changes. This creates a sense of shared ownership and responsibility, which is essential for driving continuous improvement.
In continuous improvement, everyone in the organization is encouraged to participate and contribute. Employees at all levels are encouraged to identify areas for improvement and make suggestions for how to make things better. This creates a culture of continuous improvement, where employees are empowered to make changes and improve the organization.
3rd Principle of Lean – Respect for People
Respect for People is one of the 7 principles of Lean, and it is based on the belief that all individuals have value and should be treated with dignity and respect. This principle recognizes the importance of empowering employees, creating a positive work environment, and involving employees in decision-making processes.
In organizations that practice Lean, employees are an asset, not a cost. They are encouraged to use their creativity and knowledge to improve processes, products, and services. By engaging employees in continuous improvement efforts, organizations can tap into their collective knowledge and expertise to identify areas for improvement and make changes that lead to better results.
Respect for people also involves creating a positive work environment where employees feel valued, supported, and engaged. This includes providing employees with the resources and training they need to do their jobs, creating opportunities for growth and development, and recognizing their contributions.
Involving employees in decision-making processes is another important aspect of respect for people. Employees are more likely to engage when they feel that their opinions and ideas matter. This can lead to higher levels of innovation, creativity, and problem-solving, which can ultimately improve the organization’s performance.
4th Principle of Lean – Focus on Value
Focus on Value is one of the 7 Principles of Lean and is crucial to creating a customer-centric business. This principle involves understanding customer needs and delivering products and services that meet those needs. By focusing on value, organizations can improve customer satisfaction and increase revenue.
The first step in focusing on value is to identify the customer and understand their needs and preferences. You can achieve this through direct customer feedback or market research. Once organisations understand customer needs, they can then design their processes, products and services to meet those needs. By focusing on what is important to the customer, organizations can ensure that they are delivering value that is relevant and valuable to the customer.
In addition to identifying and meeting customer needs, organizations must also continuously monitor and evaluate the value they are delivering. Organisations can do this through customer satisfaction surveys, product and service performance metrics, and market analysis. By regularly evaluating the value they are delivering, organizations can make adjustments and improvements as needed to ensure that they are meeting customer needs and delivering value in the most effective way possible.
Finally, focus on value is not just limited to the customer. It also involves a focus on delivering value to all stakeholders, including employees, shareholders, and suppliers. By delivering value to all stakeholders, organizations can create a sustainable and mutually beneficial business model that benefits everyone involved.
5th Principle of Lean – Continuous Flow
Continuous Flow is one of the 7 principles of Lean that focuses on creating a smooth and efficient flow of work processes. The goal of continuous flow is to eliminate bottlenecks and slowdowns in the production process, which can lead to increased efficiency and reduced lead times.
The first step in achieving continuous flow is to map out the production process and identify areas where bottlenecks occur. Once organisations identify the bottlenecks, they can then take steps to eliminate them, such as by re-designing processes, reducing batch sizes, or improving machine utilization. By reducing bottlenecks and creating a smoother flow, organizations can reduce lead times and improve overall efficiency.
In addition to reducing bottlenecks, continuous flow also involves creating a pull system, where production is based on customer demand, rather than forecasted demand. By using a pull system, organizations can reduce inventory and increase responsiveness to customer demand. This in turn can lead to increased customer satisfaction, as well as reduced waste and cost.
Continuous flow is not just limited to the production process. You can apply it to other areas of the organization, such as supply chain management and office processes. By applying continuous flow to these areas, organizations can improve efficiency and reduce waste in all aspects of their business.
6th Principle of Lean – Pull System
Pull is one of the 7 principles of Lean that focuses on creating a demand-driven production process, rather than a forecast-driven one. The goal of pull is to reduce inventory, increase responsiveness to customer demand, and improve overall efficiency.
The first step in implementing pull is to understand customer demand. You can achieve this through direct customer feedback or market research. Once you understand customer demand, you can then design your production process to respond to that demand. This involves creating a pull system, where production is based on actual customer demand, rather than forecasted demand.
By using a pull system, organizations can reduce inventory and increase responsiveness to customer demand. This in turn can lead to reduced waste and cost, as well as increased customer satisfaction. Pull is not just limited to the production process. You can also apply Pull to other areas of the organization, such as supply chain management and office processes.
To effectively implement pull, organizations must also establish clear communication channels between departments and stakeholders. This can involve using visual management systems, such as Kanban boards, to communicate demand and supply information. By establishing clear communication channels, organizations can ensure that everyone is working together to achieve the goal of pull.
7th Principle of Lean – Strive for Perfection
Striving for Perfection, or “Kaizen” in Japanese, is one of the 7 principles of Lean that emphasizes continuous improvement and the pursuit of excellence. It involves a never-ending journey to improve processes, products, and services, with the ultimate goal of achieving a state of perfection.
The pursuit of perfection involves the entire organization, from the CEO to the front-line workers. It encourages everyone to identify areas for improvement and make suggestions for how to make things better. This creates a culture of continuous improvement, where employees have the power to make changes and improve the organization.
One of the key elements of striving for perfection is the use of data and metrics to track progress and identify areas for improvement. By collecting and analyzing data, organizations can see where they are making progress and where they need to make changes. Organisations can then use this information to drive continuous improvement and make changes that will lead to better results.
Another key element of striving for perfection is the use of teamwork and collaboration. Teams work together to identify areas for improvement, come up with solutions, and implement changes. This creates a sense of shared ownership and responsibility, which is essential for driving continuous improvement.
Importance and Relevance of 7 Principles of Lean
The 7 principles of Lean are the foundation of Lean methodology, a continuous improvement approach. They are based on the Toyota Production System (TPS) and have been adopted by various industries worldwide. The 7 principles of lean, when applied correctly, lead to a reduction in waste, increased efficiency and higher customer satisfaction.
Despite being developed decades ago, these 7 principles of lean are still highly relevant and effective in today’s fast-paced business environment. By focusing on value, flow, pull, and continuous improvement, organizations can streamline their processes, improve quality and increase productivity.
Respect for people and the strive for perfection drive a culture of continuous improvement and create a positive work environment. Elimination of waste ensures organizations use resources effectively, reducing costs and improving profitability. By embracing these principles, organizations can create a Lean culture that drives continuous improvement, increases efficiency, and improves overall performance.
Master Lean and Six Sigma Acronyms in No Time!
The Ultimate Guide to LSS Lingo – Yours for Free
Subscribe and Get Your Hands on the Most Comprehensive List of 220+ LSS Acronyms Available. No more searching for definitions, no more confusion. Just pure expertise at your fingertips. Get your free guide and other ebooks and templates today. Download Now!
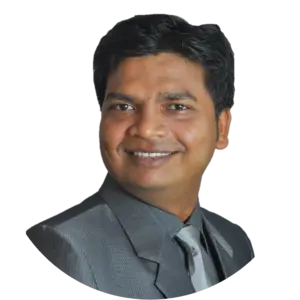
Sachin Naik
Passionate about improving processes and systems | Lean Six Sigma practitioner, trainer and coach for 14+ years consulting giant corporations and fortune 500 companies on Operational Excellence | Start-up enthusiast | Change Management and Design Thinking student | Love to ride and drive
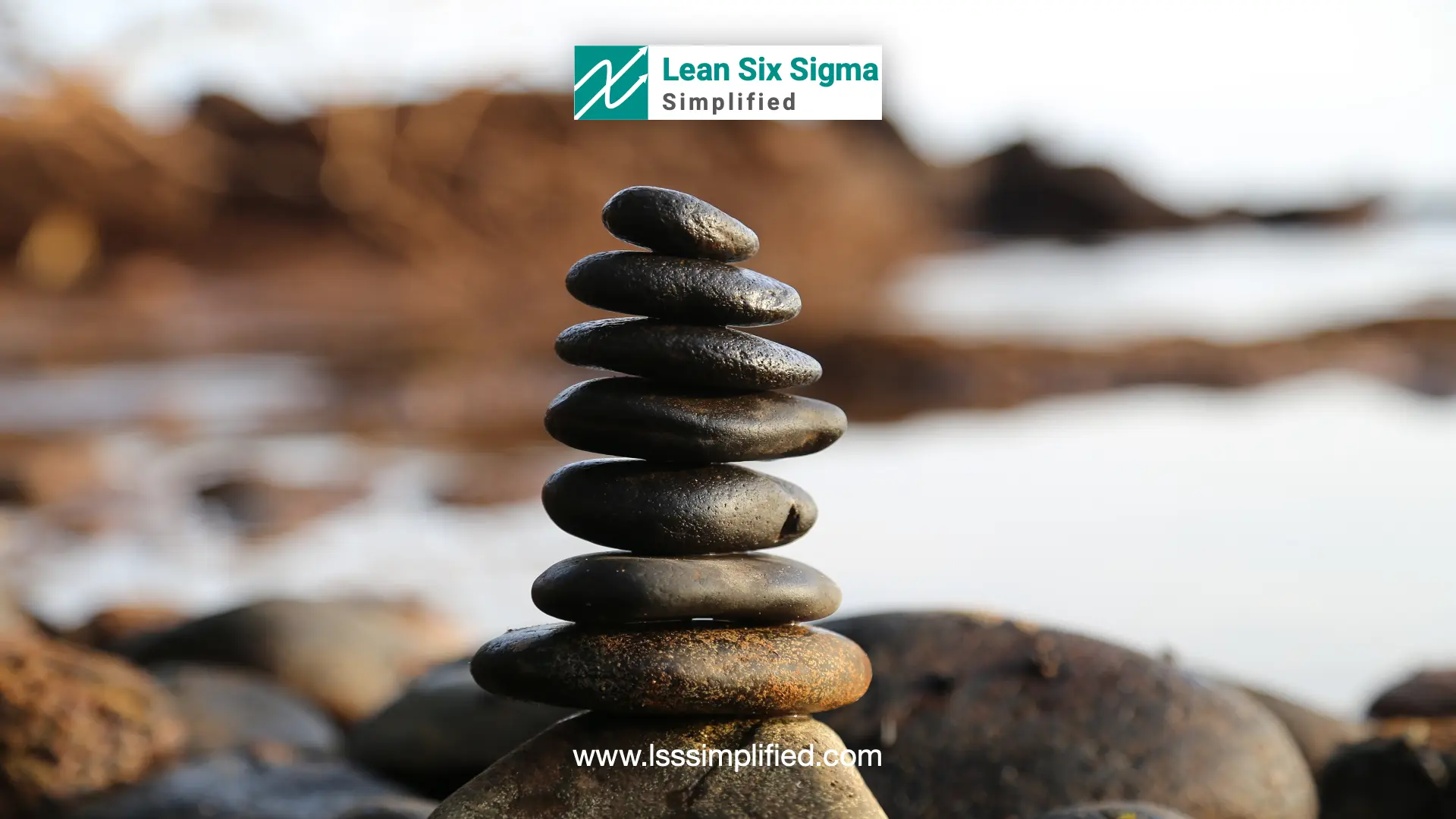
7 Principles of Lean
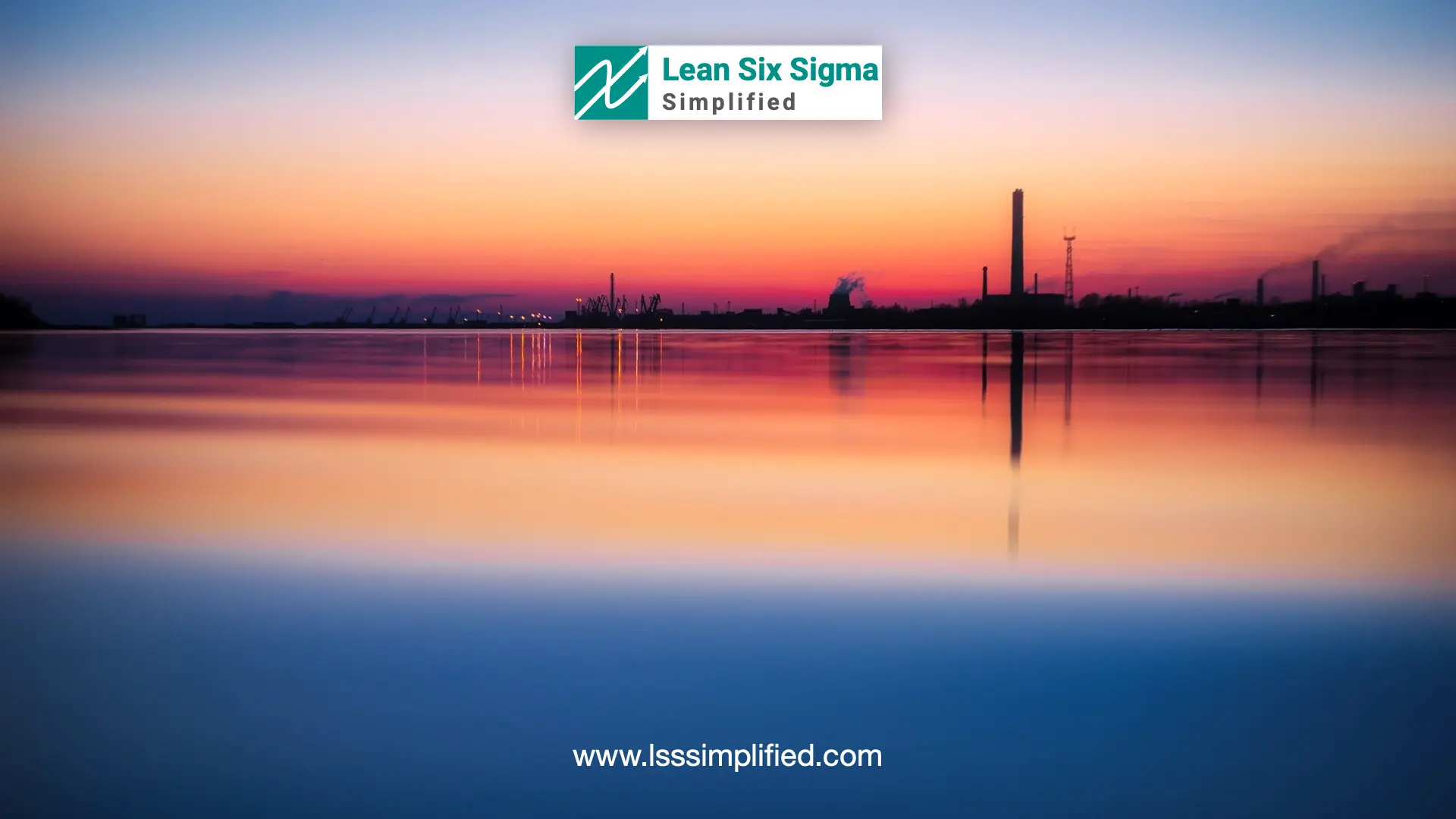
Origin of Lean

Next generation Lean Six Sigma – Harnessing the Power of AI

What is Lean Six Sigma and how it helps your career
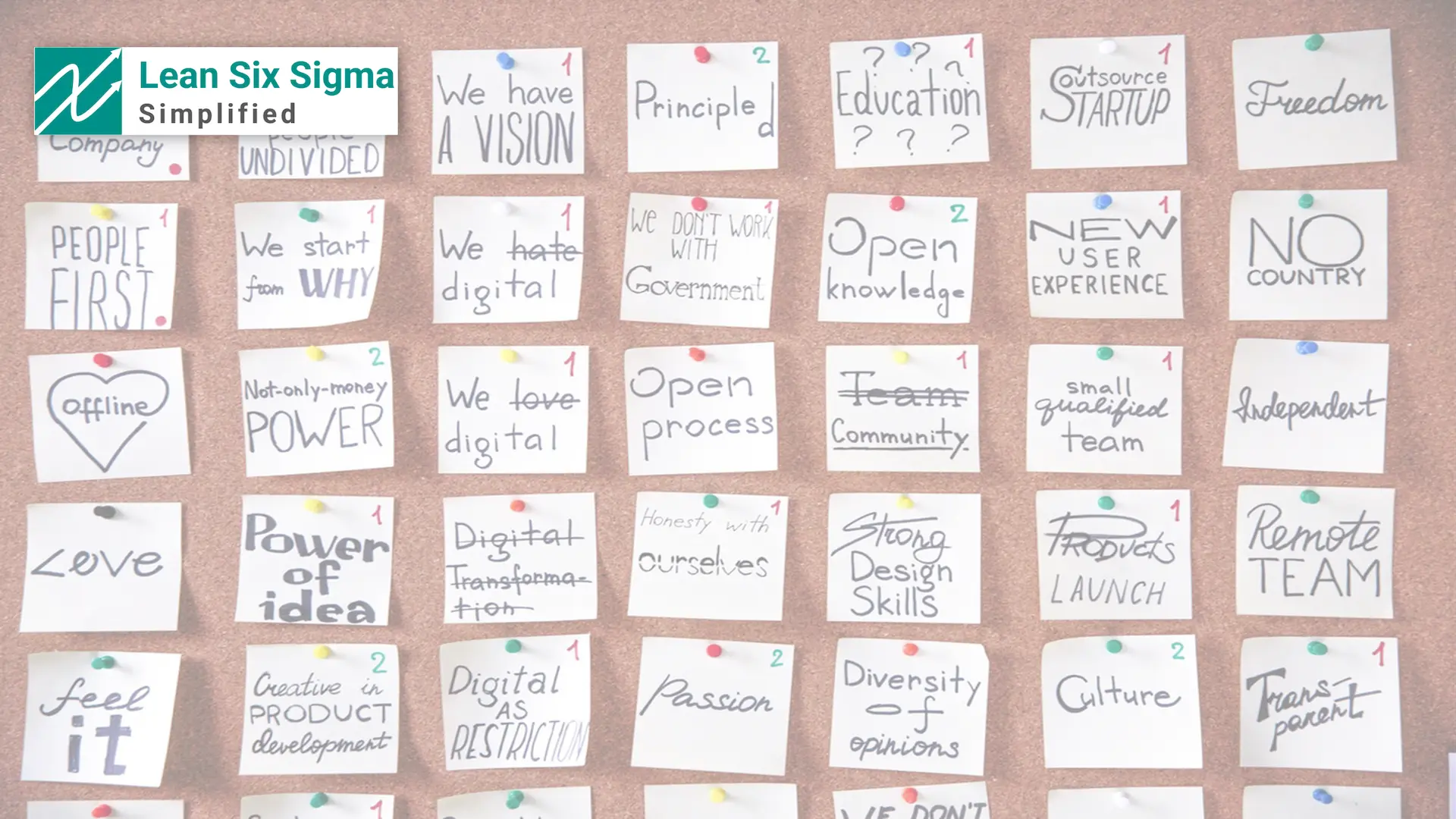
Nominal Group Technique Definition, Examples Steps
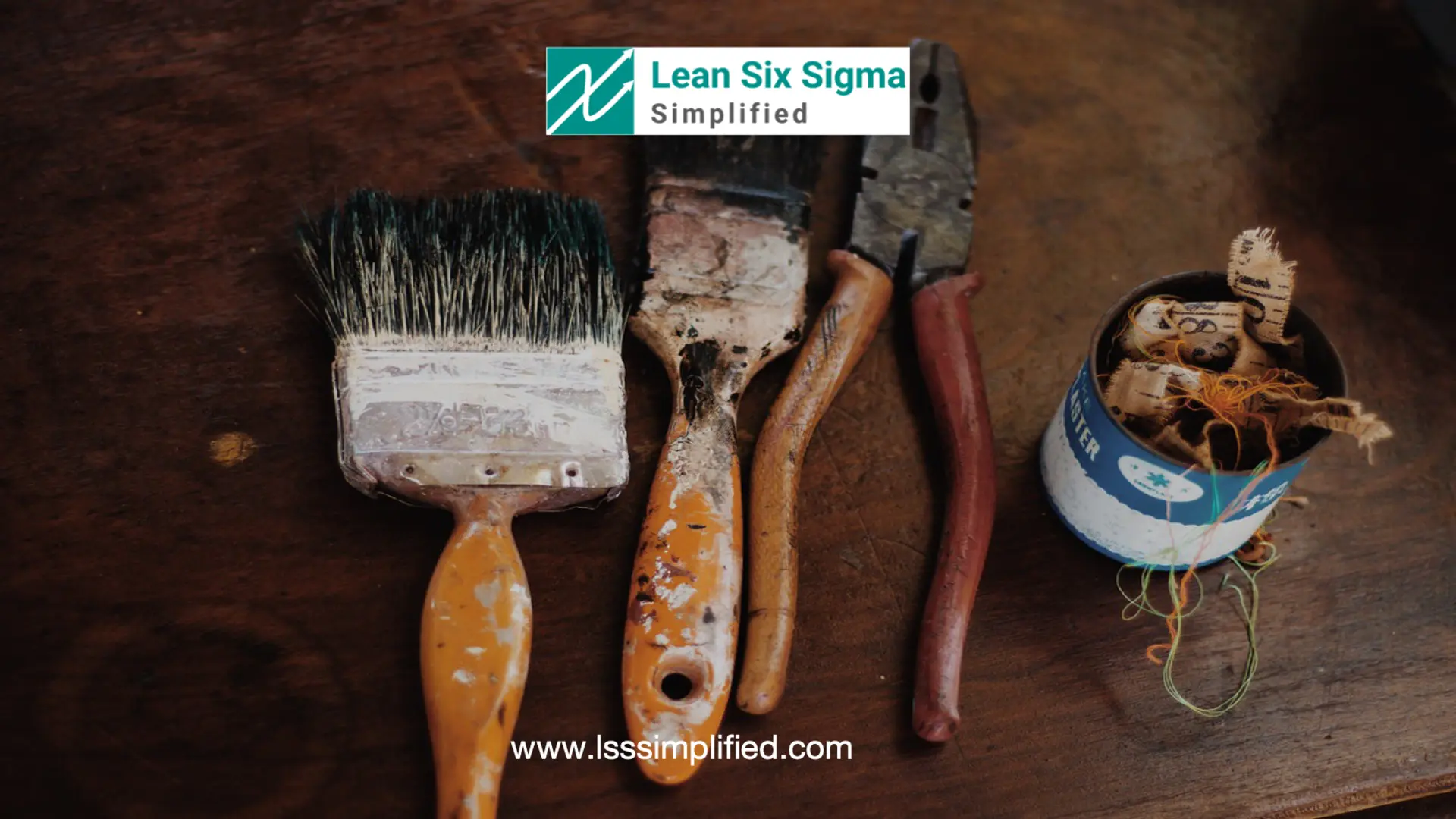
What are the measures of Variation

What are the measures of Central Tendency
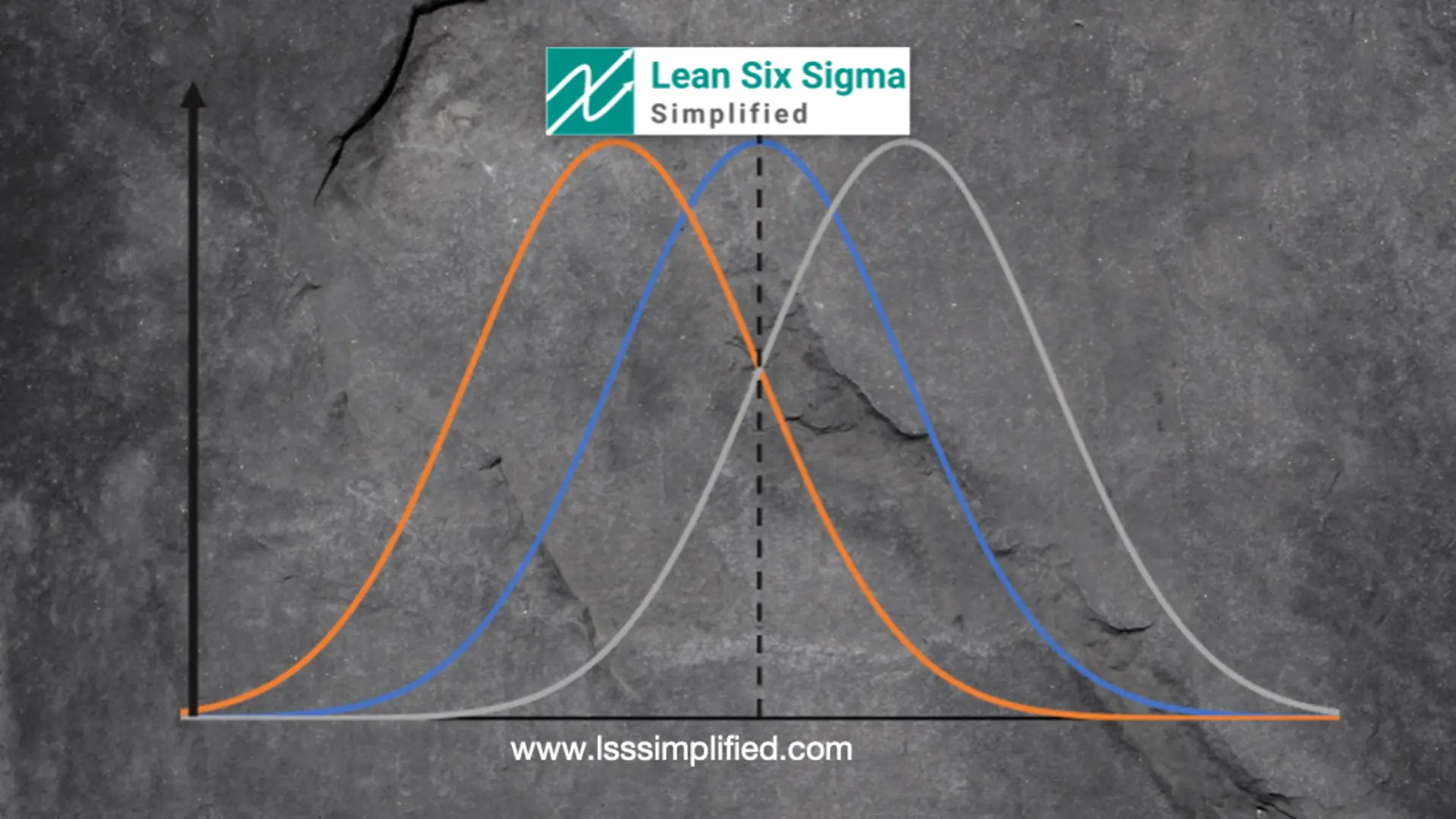
Normal Distribution for Lean Six Sigma

Probability Distribution for Lean Six Sigma
