Back flushing is a technique used in inventory management. It helps companies reduce the amount of raw materials and work-in-progress (WIP) inventory they keep on hand. Back flushing allows the inventory system to automatically calculate the amount of raw materials needed for production. By doing so, back flushing reduces the need for manual calculations and the risk of inventory errors. In this article, we will explore back flushing in detail, including how it works, its benefits and drawbacks, and how to implement it in your own inventory management system.
What is Back Flushing?
Back flushing is a production-driven method of inventory management. It is used to calculate the amount of raw materials required to produce a finished product. The idea behind Back Flushing is that the raw materials required to produce a product are consumed as the product is being manufactured. As the production process progresses, the inventory system automatically calculates the amount of raw materials that have been used and updates the inventory accordingly.
The back flushing process typically starts with the completion of a finished product. You update the inventory system post completion of finished product to reflect the amount of raw materials used in the production of that product. The system calculates the amount of raw materials required based on production batch size and the standard bill of materials. The raw materials are then “flushed” out of inventory and replaced with the finished product.
Benefits of Back Flushing
Reduced Inventory Costs
Back flushing can help reduce inventory costs by reducing the amount of raw materials and WIP inventory. This is because the inventory system is able to automatically calculate the amount of raw materials required for production. This eliminates the need for manual calculations and reducing the risk of inventory errors.
Improved Accuracy
Back flushing can improve accuracy in inventory management by reducing the risk of human error in manual calculations. The automatic calculation of raw materials required for production eliminates the need for manual calculations, reducing the risk of errors in the inventory system.
Increased Efficiency
Back flushing can increase efficiency in inventory management by reducing the time and resources required to manage inventory. The automatic calculation of raw materials required for production eliminates the need for manual calculations, freeing up time and resources for other tasks.
Better Visibility
Back flushing can provide better visibility into the inventory system by providing real-time updates on the amount of raw materials and WIP inventory. This helps companies to better manage their inventory and ensure that they have the raw materials they need to meet production demands.
Drawbacks of Back Flushing
Dependence on Accurate Bill of Materials
Back flushing depends on an accurate bill of materials (BOM) to calculate the amount of raw materials required for production. If the BOM is inaccurate, the inventory system may calculate the wrong amount of raw materials, leading to overstocking or stock shortages.
Inaccurate Inventory Tracking
Back flushing may result in inaccurate inventory tracking if there are discrepancies in the production process. For example, if raw materials are used in the production of multiple products, the inventory system may not accurately reflect the amount of raw materials used for each product.
Complexity
Back flushing can be a complex process, particularly for companies with a large number of products and raw materials. Implementing back flushing in an inventory management system can require significant resources and technical expertise.
How to Implement Back Flushing
Determine the Appropriate Products
The first step in implementing back flushing is to determine which products are appropriate for the process. Products that have a stable production process and a consistent bill of materials are typically good candidates for back flushing. It may also be helpful to consider the volume of production for each product to determine if back flushing will provide significant benefits.
Develop an Accurate Bill of Materials
A key component of back flushing is an accurate bill of materials (BOM) for each product. The BOM should include a list of all raw materials required for production. It should also include the standard quantities needed for each product. It is important to regularly review and update the BOM. This is to ensure its accuracy and reflect any changes in the production process.
Integrate Back Flushing into the Inventory Management System
Once the BOM is in place, the next step is to integrate back flushing into the inventory management system. You can do it by by modifying the existing system or by implementing a new system equipped for back flushing. It is important to work with a knowledgeable provider to ensure proper configuration of the system. And too ensure that the configuration meets the specific needs of your company.
Implement a Testing and Validation Process
Before implementing back flushing, it is important to thoroughly test and validate the system to ensure that it is working correctly. This may include testing the system with a small sample of products to verify that the inventory updates are accurate and that the system is properly calculating the amount of raw materials required for production.
Monitor and Optimize the Process
Once back flushing is implemented, it is important to monitor the process to ensure that it is working as expected and to identify any areas for improvement. This may include reviewing the inventory updates to ensure that they are accurate, and making adjustments to the BOM or the production process to optimize the system.
Back flushing is a powerful technique for managing inventory that can help companies reduce inventory costs, improve accuracy, increase efficiency, and provide better visibility into their inventory systems. To successfully implement back flushing, companies need to have an accurate bill of materials, integrate the process into their inventory management system, and monitor the process to ensure that it is working as expected. By following these steps, companies can realize significant benefits from back flushing and improve their overall inventory management process.
Master Lean and Six Sigma Acronyms in No Time!
The Ultimate Guide to LSS Lingo – Yours for Free
Subscribe and Get Your Hands on the Most Comprehensive List of 220+ LSS Acronyms Available. No more searching for definitions, no more confusion. Just pure expertise at your fingertips. Get your free guide and other ebooks and templates today. Download Now!
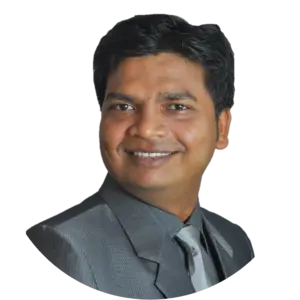
Sachin Naik
Passionate about improving processes and systems | Lean Six Sigma practitioner, trainer and coach for 14+ years consulting giant corporations and fortune 500 companies on Operational Excellence | Start-up enthusiast | Change Management and Design Thinking student | Love to ride and drive
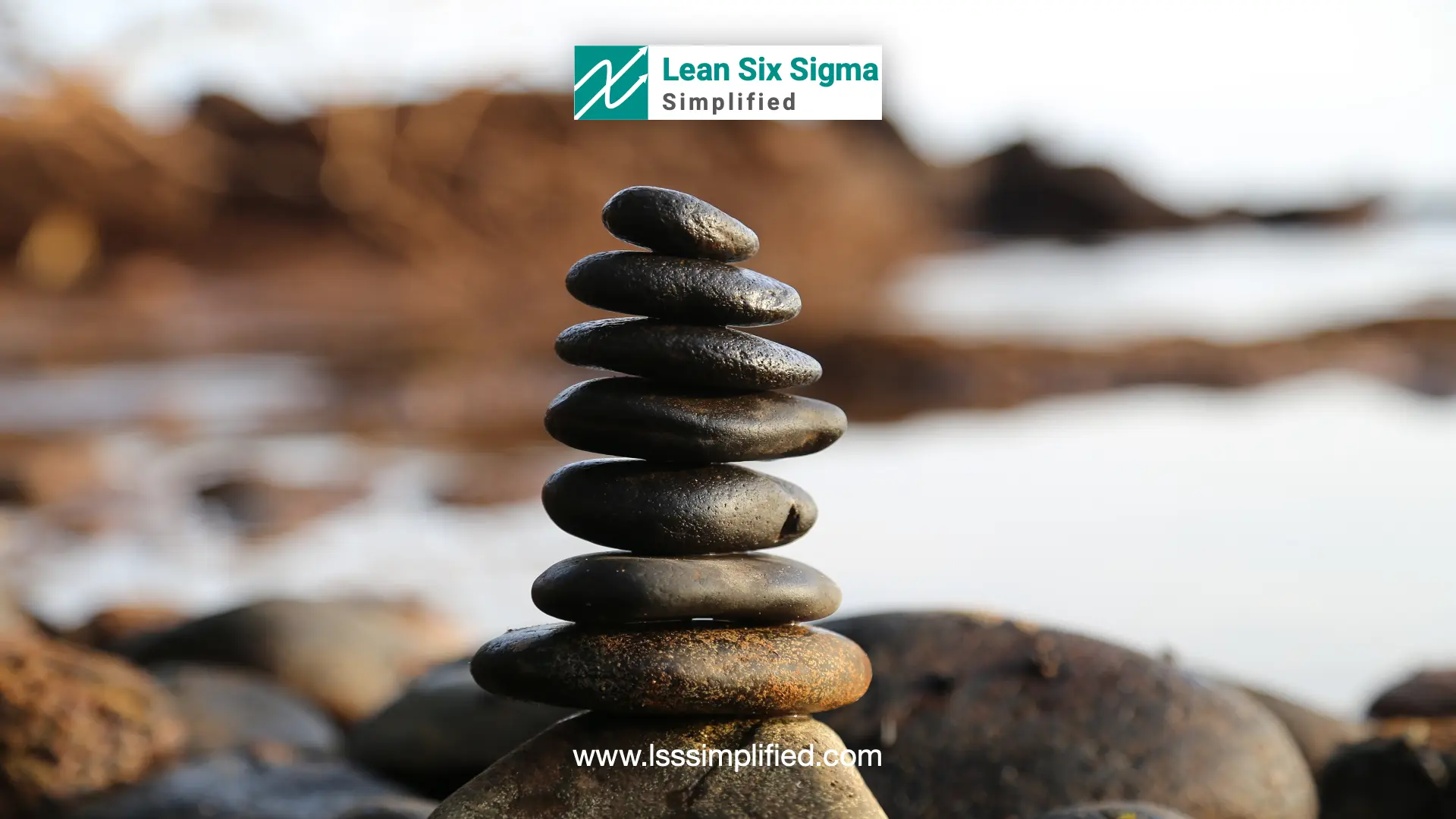
7 Principles of Lean
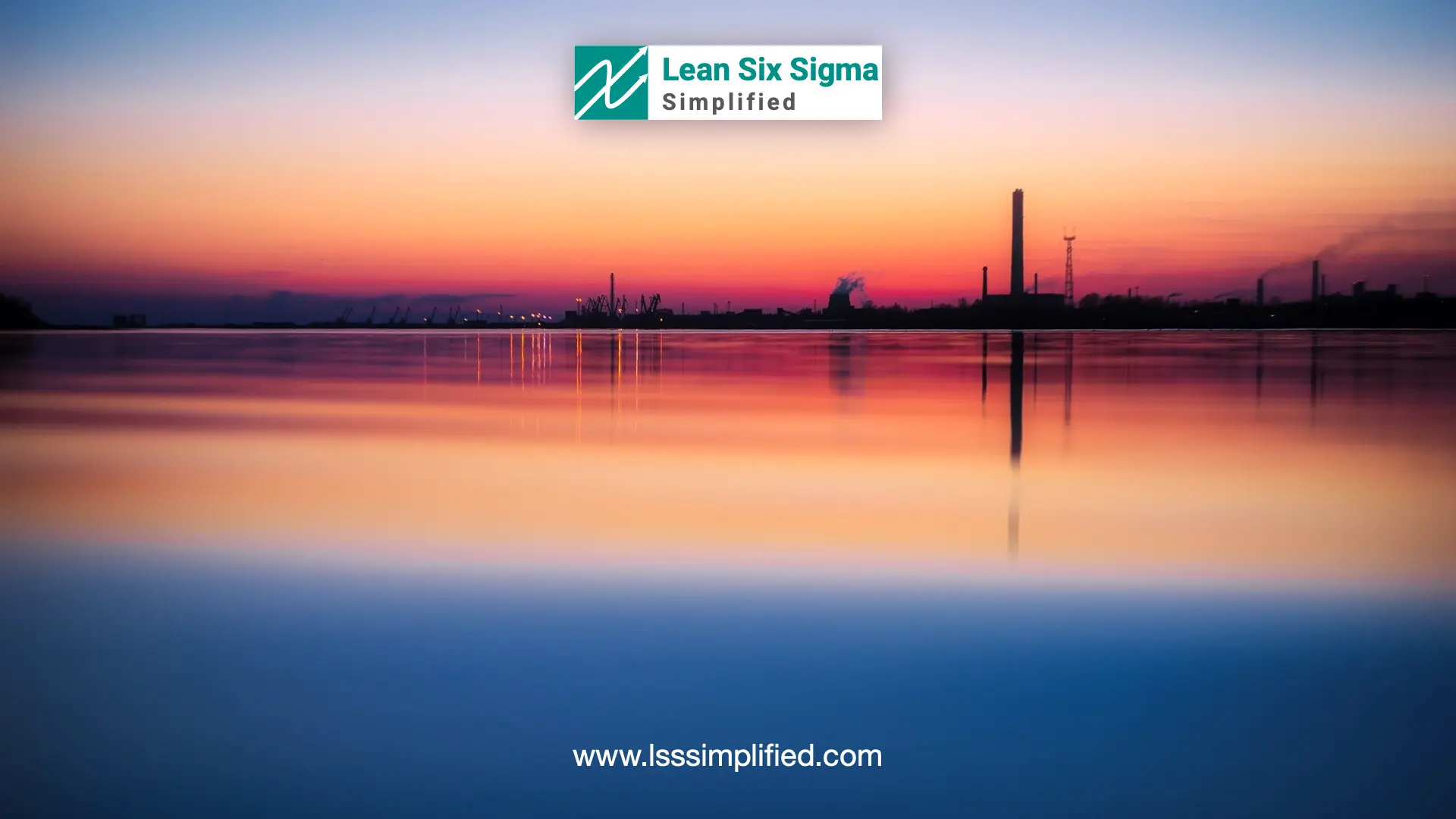
Origin of Lean

Next generation Lean Six Sigma – Harnessing the Power of AI

What is Lean Six Sigma and how it helps your career
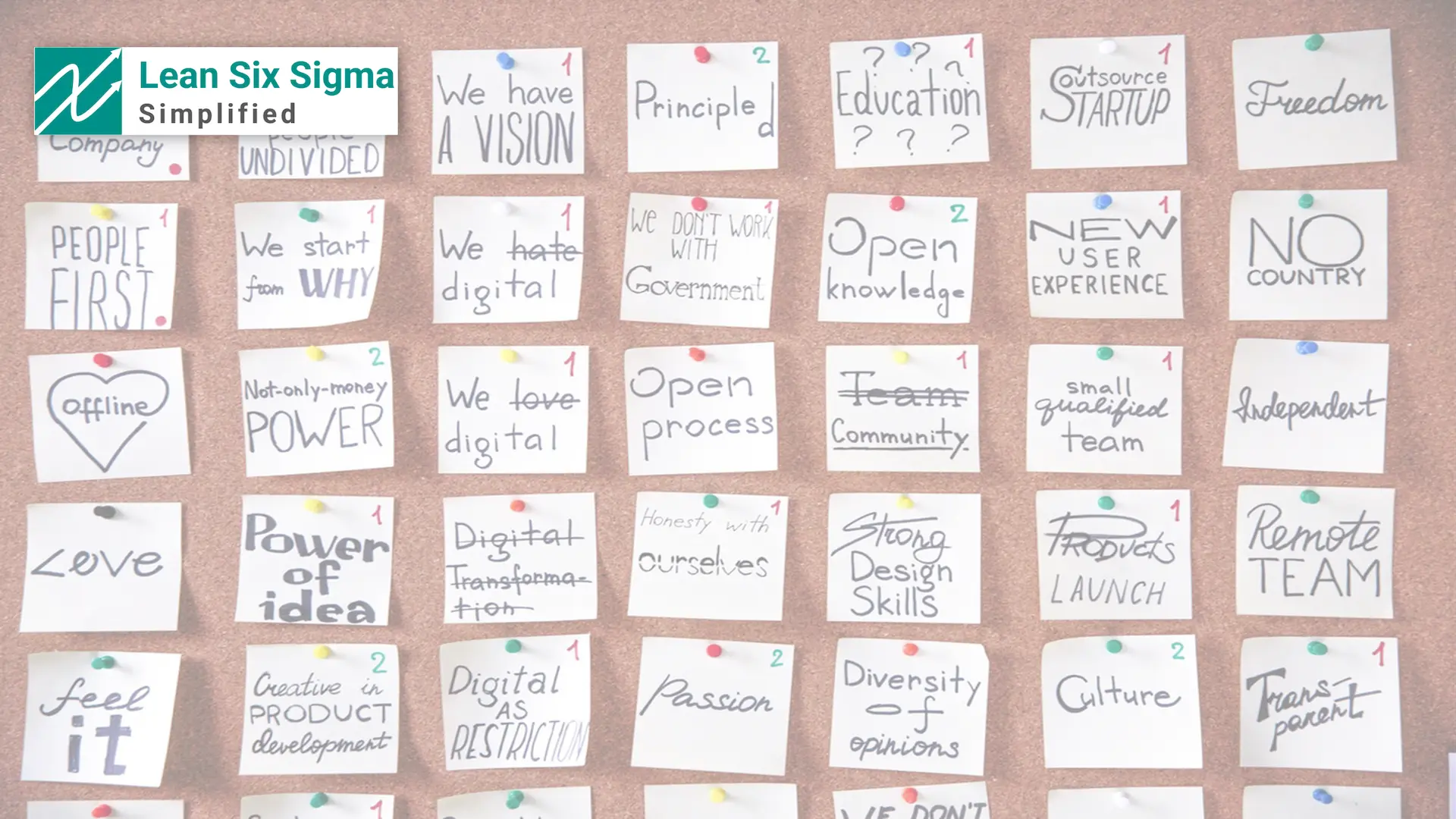
Nominal Group Technique Definition, Examples Steps
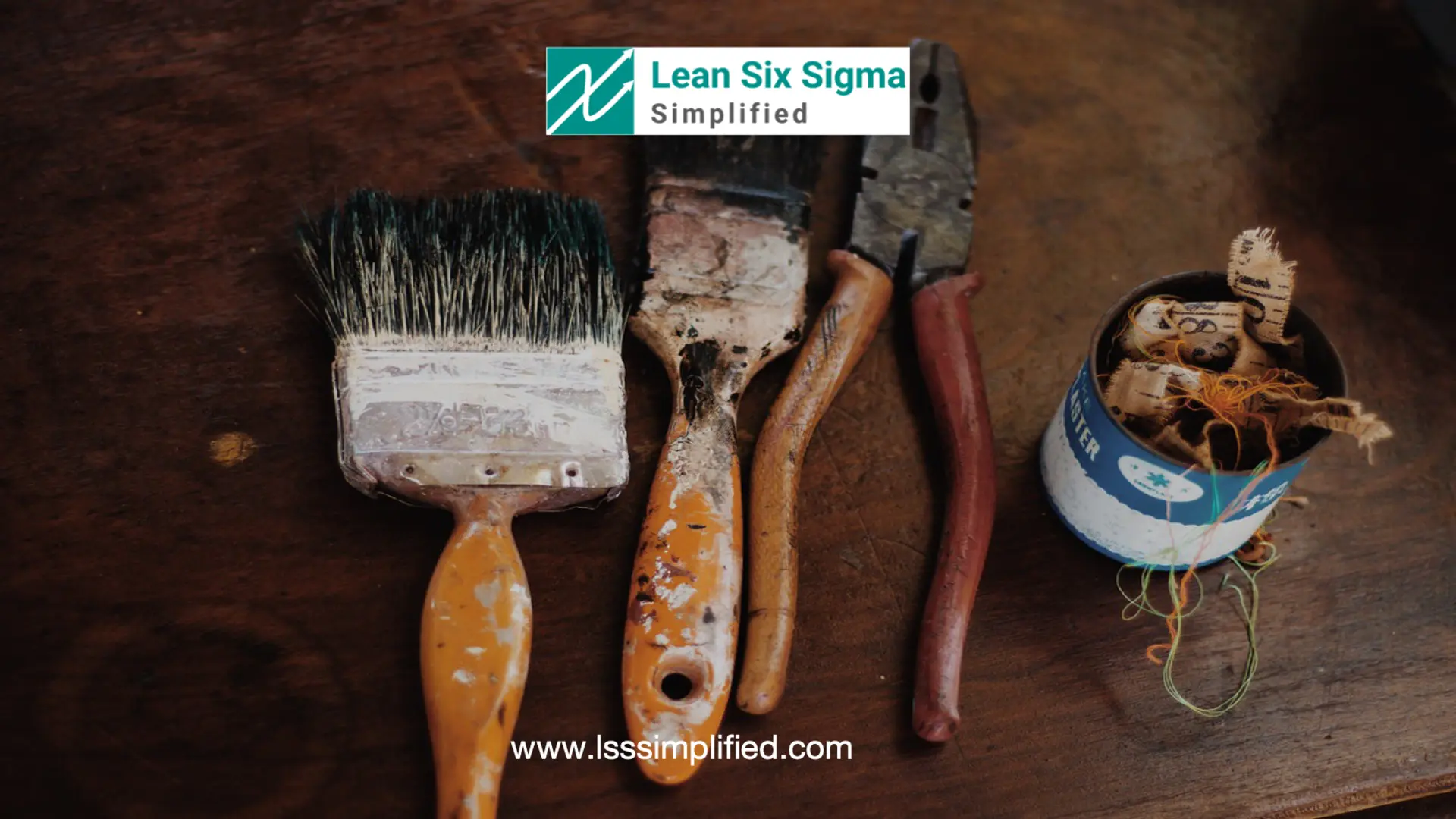
What are the measures of Variation

What are the measures of Central Tendency
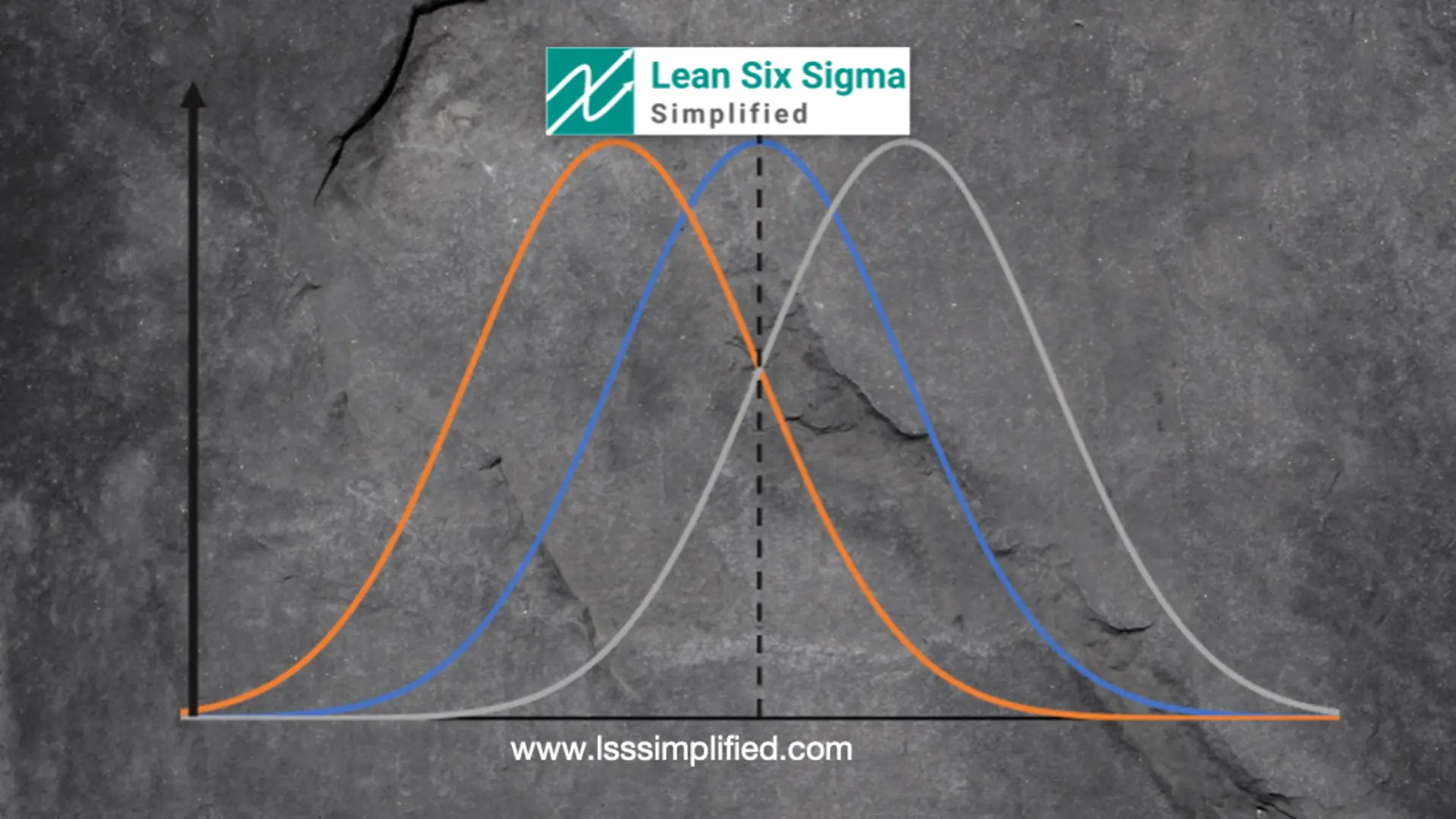
Normal Distribution for Lean Six Sigma

Probability Distribution for Lean Six Sigma
