Andon board is a visual management tool used in manufacturing and assembly lines to quickly identify and communicate problems to the relevant personnel. They are designed to improve the efficiency of production processes and to reduce downtime. In this blog post, we will explore the different aspects of Andon boards, including their history, components, and benefits.
History of Andon Boards
The concept of Andon boards originated in Japan during the 20th century. The term “Andon” refers to a traditional Japanese paper lantern. In manufacturing, Andon boards were first implemented by Toyota in the 1950s as part of the company’s “Just-In-Time” production system. The goal was to quickly identify and solve problems on the assembly line, in order to improve efficiency and reduce downtime.
Components of an Andon Board
An Andon board typically includes several key components:
- A visual display: This is usually a large screen or monitor that displays real-time information about the production process.
- Status indicators: These are typically lights or LEDs that indicate the current status of the production line (e.g. “running,” “stopped,” “problem”).
- Alarm systems: Andon boards often include an alarm system that sounds when a problem is detected, alerting personnel to take action.
- Control buttons: These buttons are useful to manually activate the alarm system or to communicate with other personnel.
Types of Andon Boards
There are several types of Andon boards, each with its own unique features and benefits. Some of the most common types of Andon boards include:
- Manual Andon boards: These boards rely on manual input from personnel to activate the alarm system and communicate problems. They are typically less expensive than other types of Andon boards and are suitable for small-scale operations.
- Automatic Andon boards: These boards use sensors and other technology to automatically detect problems and activate the alarm system. They are more expensive than manual Andon boards but provide more accurate and real-time information.
- Hybrid Andon boards: These boards combine the features of manual and automatic Andon boards, allowing for both manual and automatic input. They are suitable for larger operations and provide more flexibility than manual or automatic Andon boards.
Process of Implementing Andon Board
Implementing Andon boards in a manufacturing facility requires careful planning and execution. The process typically includes the following steps:
- Define the objectives: The first step is to clearly define the objectives of implementing Andon boards in the facility. This includes identifying the specific problem areas that Andon boards are intended to address.
- Conduct a feasibility study: A feasibility study is conducted to determine the feasibility of implementing Andon boards in the facility. This includes assessing the cost and resources required, as well as the potential benefits.
- Select the appropriate type of Andon board: Based on the objectives and the feasibility study, the appropriate type of Andon board is selected. This will depend on the specific needs of the facility and the resources available.
- Design and install the Andon board: The Andon board is designed and installed in the facility. This includes setting up the display, status indicators, alarm systems, and control buttons.
- Train personnel: Personnel are trained on how to use and interpret the Andon board. This includes understanding the different status indicators and the procedures for activating the alarm system.
- Monitor and evaluate: The effectiveness of the Andon board is monitored and evaluated over time. This includes tracking key performance indicators and making adjustments as needed.
Benefits of Andon Boards
Andon boards have several key benefits:
- Improved efficiency: Andon boards help to identify and solve problems on the assembly line quickly, reducing downtime and increasing overall efficiency.
- Increased visibility: Andon boards provide real-time information about the production process, allowing personnel to quickly identify issues and take action.
- Better communication: Andon boards facilitate communication between different departments and personnel, improving collaboration and problem-solving.
- Reduced costs: Andon boards can help to reduce costs by reducing downtime and increasing overall efficiency.
Andon boards are an essential tool for modern manufacturing and assembly lines. By providing real-time information, facilitating communication, and reducing downtime, Andon boards help to improve efficiency and reduce costs. While the concept of Andon boards originated in Japan, they are now used in manufacturing facilities all around the world, and continue to be an important part of modern production processes.
Master Lean and Six Sigma Acronyms in No Time!
The Ultimate Guide to LSS Lingo – Yours for Free
Subscribe and Get Your Hands on the Most Comprehensive List of 220+ LSS Acronyms Available. No more searching for definitions, no more confusion. Just pure expertise at your fingertips. Get your free guide and other ebooks and templates today. Download Now!
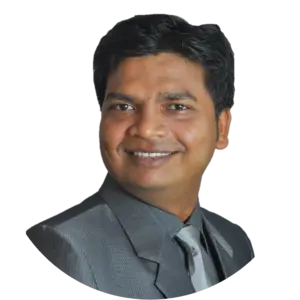
Sachin Naik
Passionate about improving processes and systems | Lean Six Sigma practitioner, trainer and coach for 14+ years consulting giant corporations and fortune 500 companies on Operational Excellence | Start-up enthusiast | Change Management and Design Thinking student | Love to ride and drive
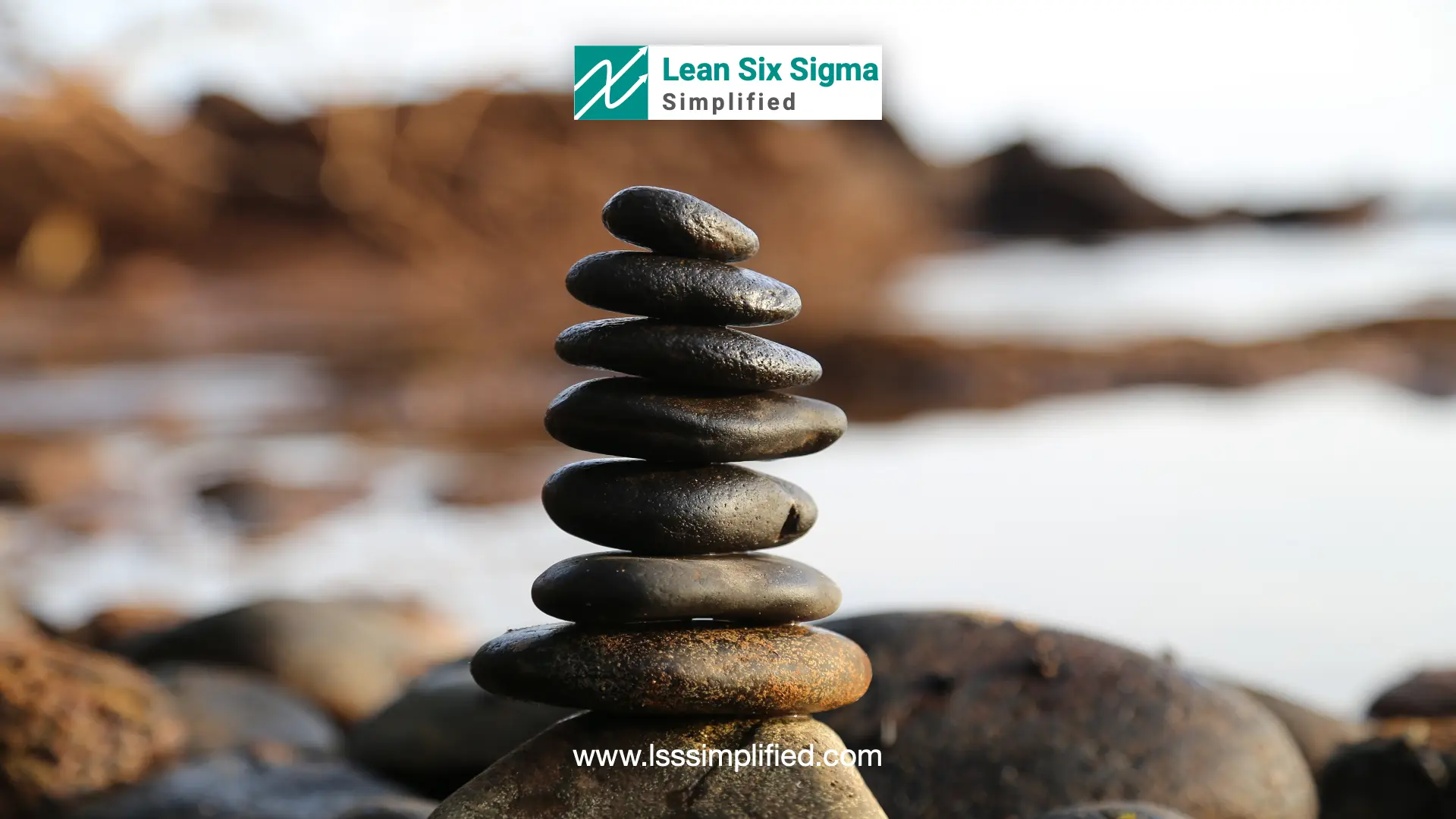
7 Principles of Lean
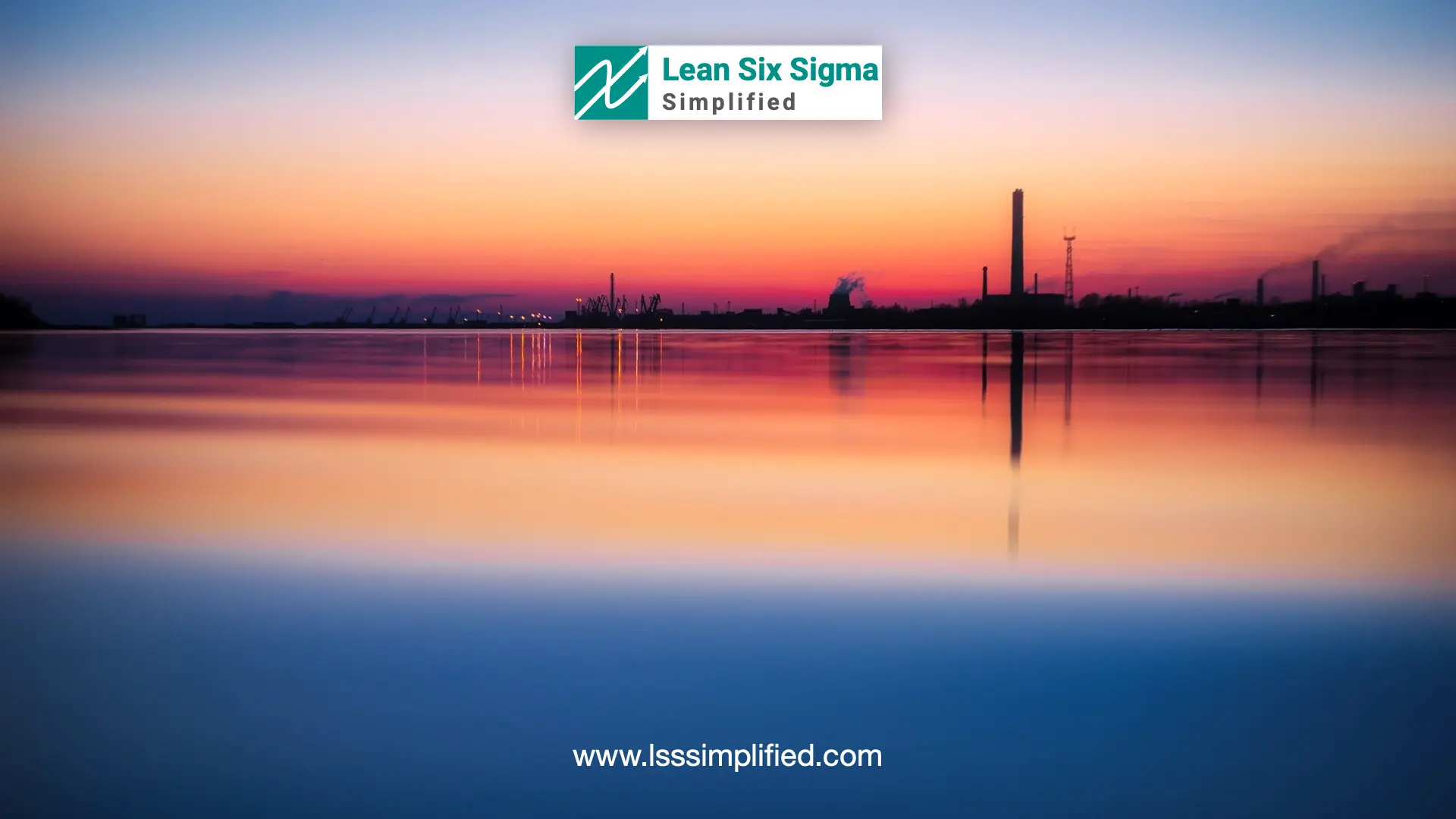
Origin of Lean

Next generation Lean Six Sigma – Harnessing the Power of AI

What is Lean Six Sigma and how it helps your career
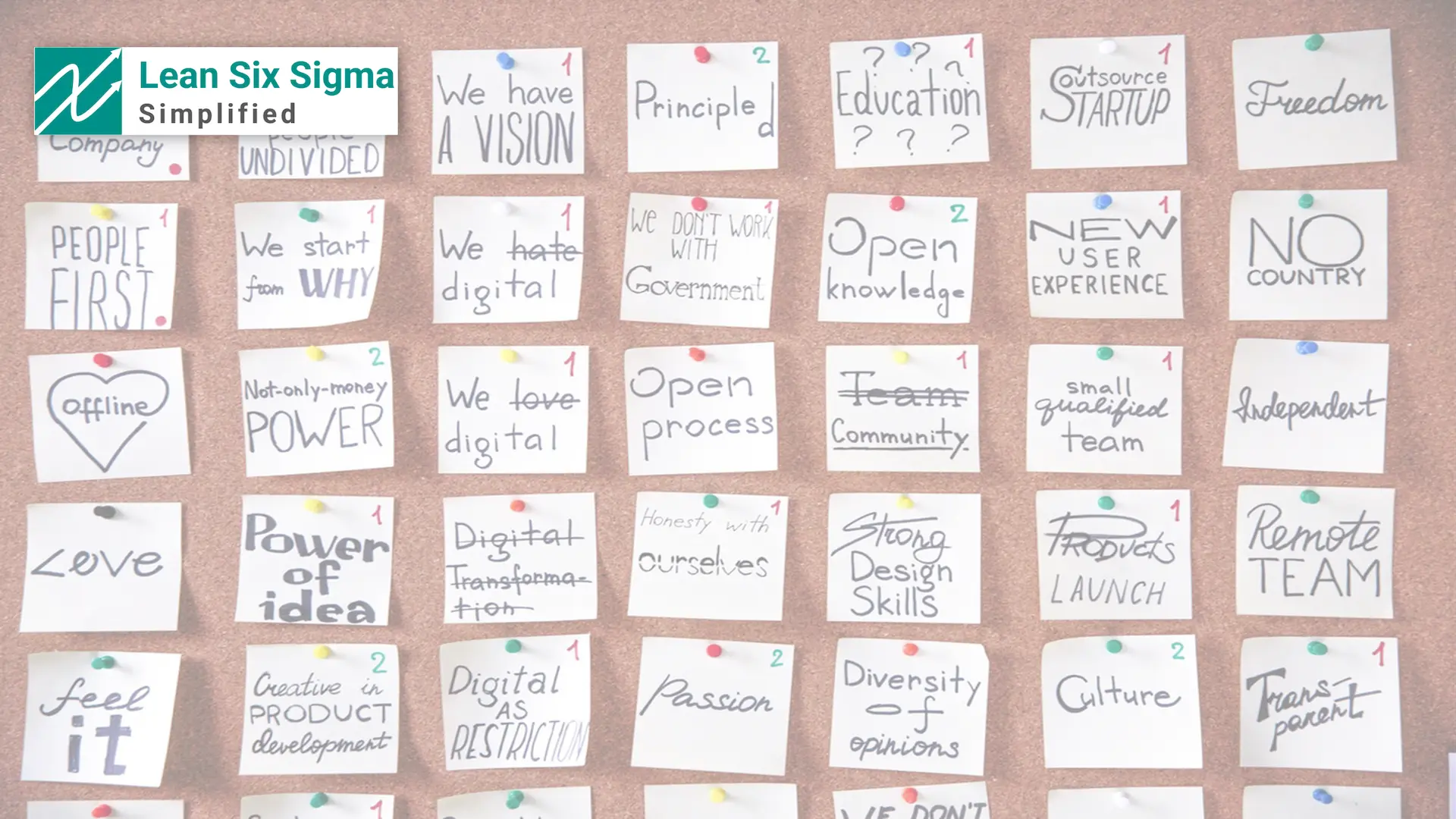
Nominal Group Technique Definition, Examples Steps
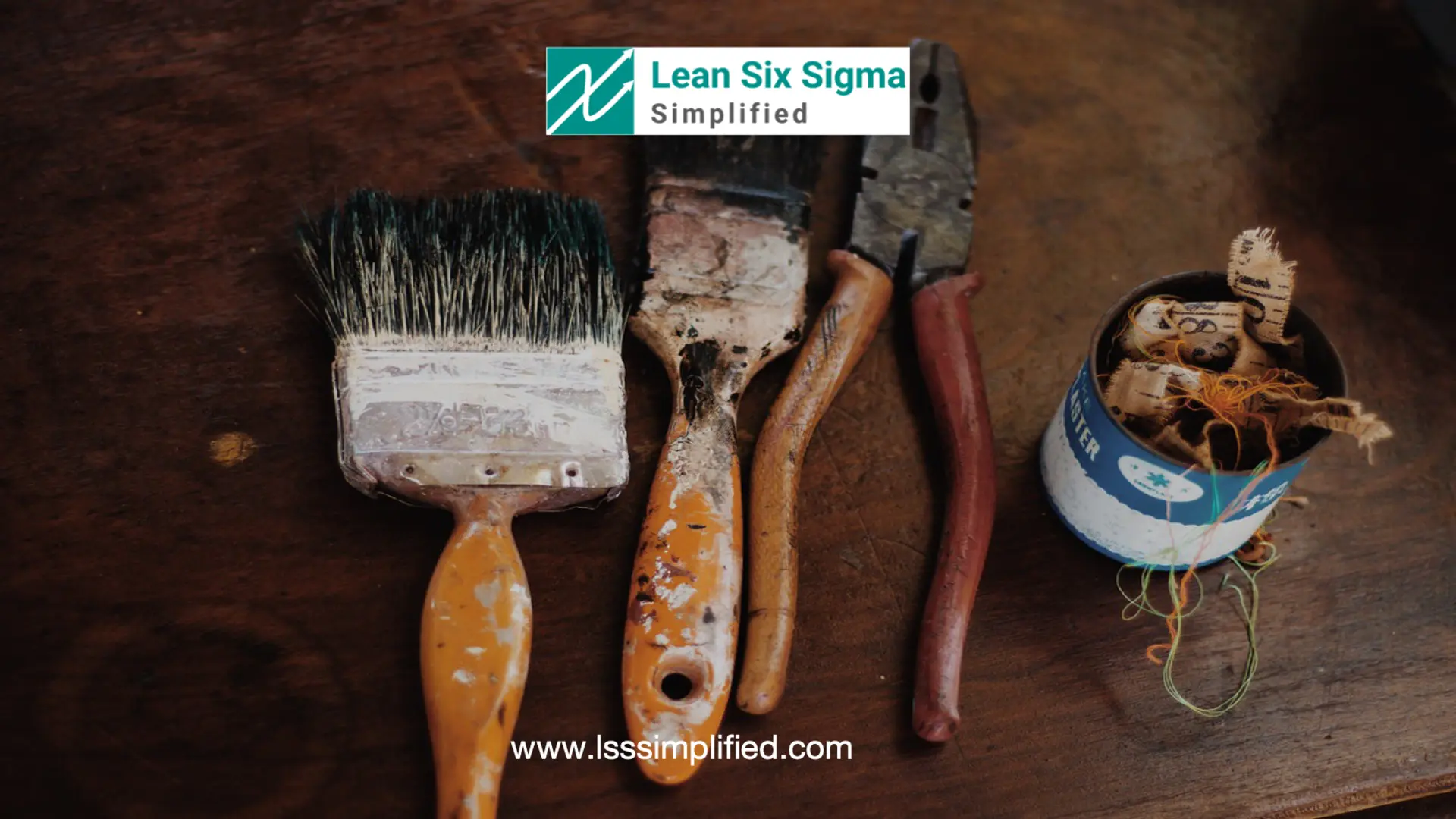
What are the measures of Variation

What are the measures of Central Tendency
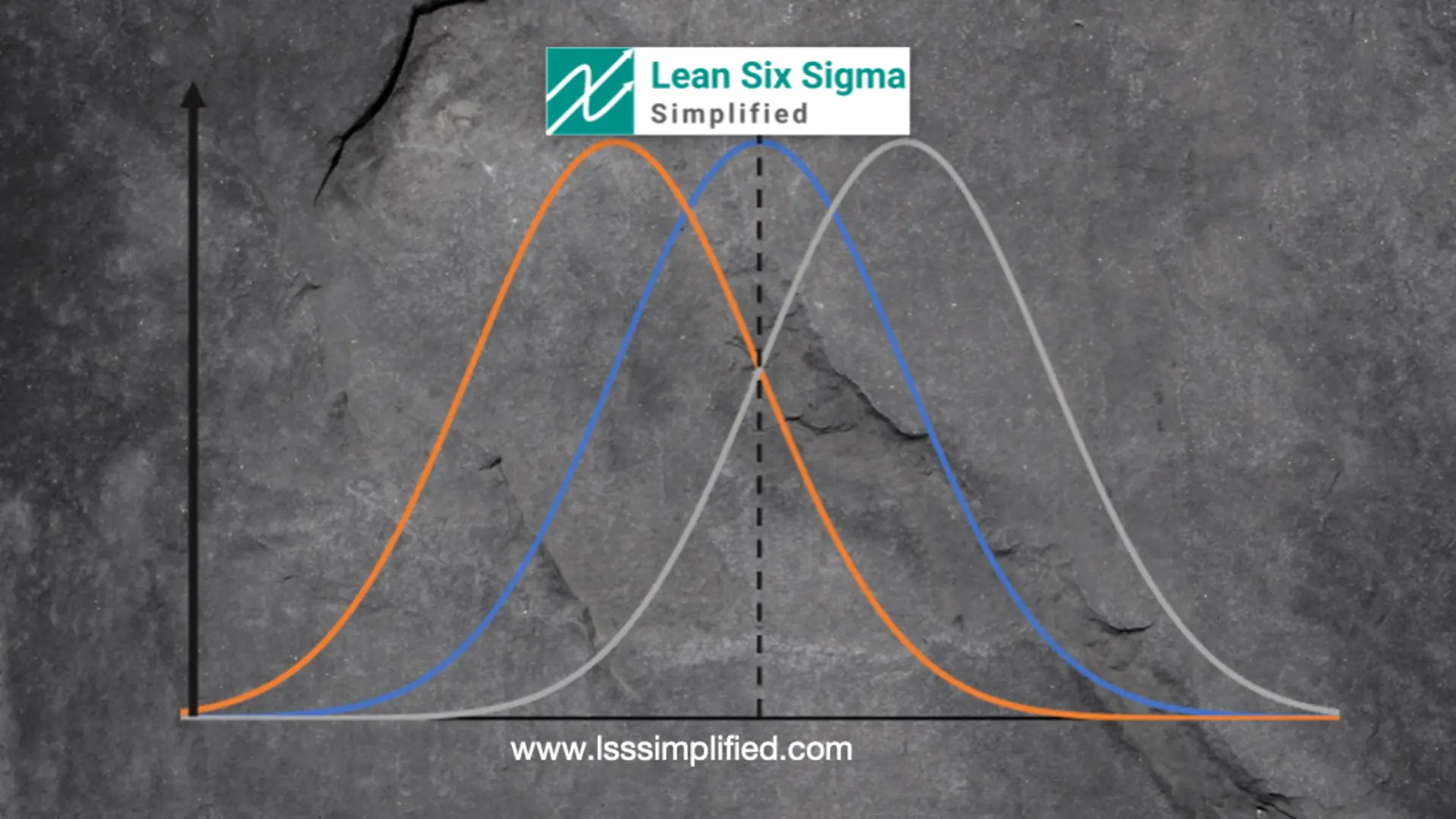
Normal Distribution for Lean Six Sigma

Probability Distribution for Lean Six Sigma
