Acceptable Quality Level (AQL) is a statistical measurement used in the quality control process to determine the number of defective units in a production batch that are considered acceptable. It is a performance standard that serves as a guide for inspecting and accepting or rejecting a batch of products. Acceptable Quality Level is also known as the “Acceptable Quality Limit” (AQL), and it serves as a quality control metric that is used to define the maximum number of defective units that can be found in a production batch.
Methodology
Acceptable Quality Level is determined by performing a random sampling of a batch of products and then inspecting them for defects. The number of defective units found in the sample is then compared to the AQL to determine if the batch of products is acceptable or not. The AQL is typically expressed as a percentage or ratio, with a lower AQL indicating a higher level of quality.
Acceptable Quality Level is determined by taking into account both the cost of inspecting and rejecting a batch of products. It takes into account the cost of shipping and handling defective units as well. Therefore, the AQL is typically set at a level that balances these two costs.
Acceptable Quality Level is also used to determine the sample size required for inspection. The sample size is based on the AQL level, and is determined by using statistical tables or software.
Benefits of Acceptable Quality Level
- Acceptable Quality Level is a useful tool for controlling and managing quality in a production process.
- It helps to ensure that products meet a minimum level of quality, and that defective units are identified and addressed.
- It also helps to reduce costs by balancing the cost of inspecting and rejecting a batch of products against the cost of shipping and handling defective units.
- Acceptable Quality Level is useful for determining the sample size for inspection, which helps to ensure that a representative sample is inspected.
Implementation of Acceptable Quality Level
Implementing Acceptable Quality Level requires a clear understanding of the production process and the costs involved in inspecting and rejecting a batch of products, as well as the cost of shipping and handling defective units. It also requires the use of statistical tables or software to determine the sample size for inspection.
It is important to have a clear understanding of the AQL level, and to communicate it effectively to all stakeholders involved in the production process. This includes management, production workers, and quality control personnel. Regular monitoring and follow-up are also necessary to ensure that the AQL is being met and that the production process is operating at an optimal level.
AQL is also used in conjunction with other quality control metrics such as Six Sigma, Total Quality Management (TQM) and ISO 9001. These methodologies provide a comprehensive approach to quality management, and Acceptable Quality Level is used as one of the tools to measure and maintain quality standards.
Limitations of AQL
- AQL is based on statistical measurements and is therefore subject to variations in the production process.
- It also assumes that the cost of inspecting and rejecting a batch of products is known, which may not always be the case.
- It also assumes that the sample size is large enough to be representative of the entire batch of products, which may not always be the case.
Acceptable Quality Level (AQL) is an important tool for controlling and managing quality in a production process. It helps to ensure that products meet a minimum level of quality and that defective units are identified and addressed. However, it is important to consider the limitations of AQL and to use it in conjunction with other quality control metrics such as Six Sigma, Total Quality Management (TQM) and ISO 9001. AQL is based on statistical measurements and its implementation requires a clear understanding of the production process and the costs involved in inspecting and rejecting a batch of products, as well as the cost of shipping and handling defective units. Regular monitoring and follow-up are also necessary to ensure that the Acceptable Quality Level is being met and that the production process is operating at an optimal level.
Master Lean and Six Sigma Acronyms in No Time!
The Ultimate Guide to LSS Lingo – Yours for Free
Subscribe and Get Your Hands on the Most Comprehensive List of 220+ LSS Acronyms Available. No more searching for definitions, no more confusion. Just pure expertise at your fingertips. Get your free guide and other ebooks and templates today. Download Now!
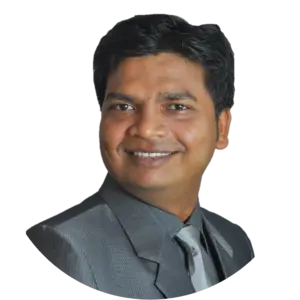
Sachin Naik
Passionate about improving processes and systems | Lean Six Sigma practitioner, trainer and coach for 14+ years consulting giant corporations and fortune 500 companies on Operational Excellence | Start-up enthusiast | Change Management and Design Thinking student | Love to ride and drive
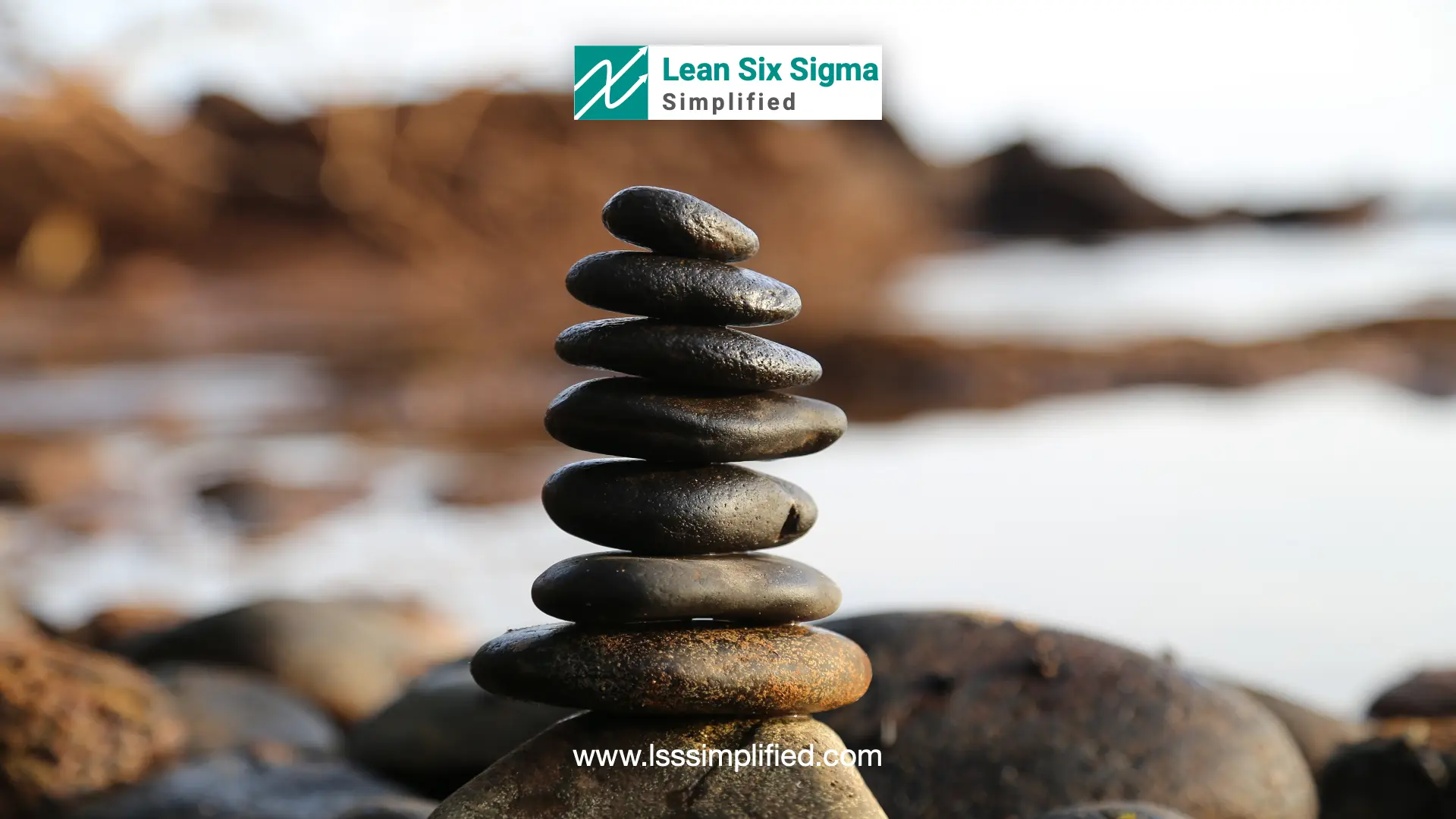
7 Principles of Lean
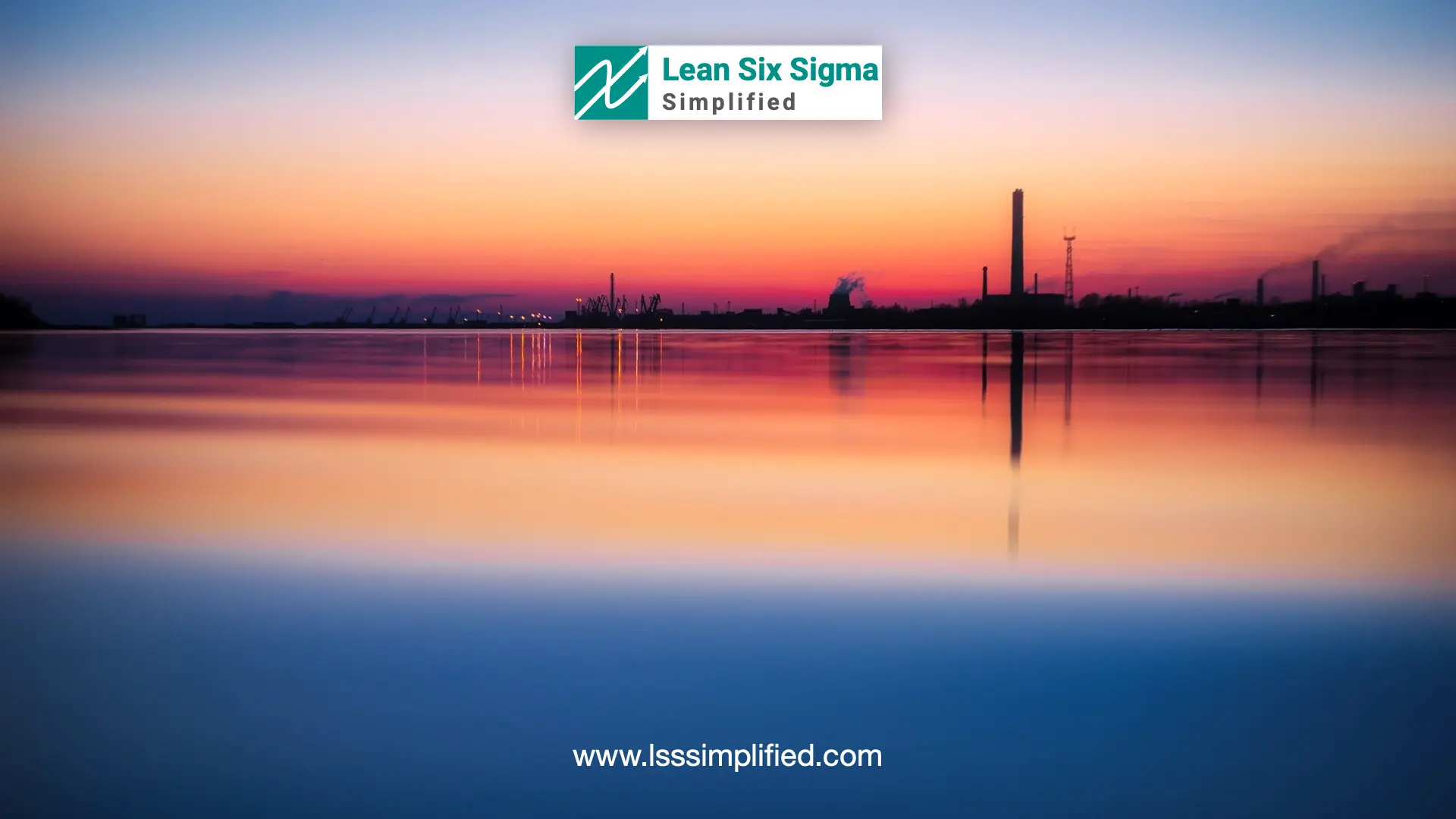
Origin of Lean

Next generation Lean Six Sigma – Harnessing the Power of AI

What is Lean Six Sigma and how it helps your career
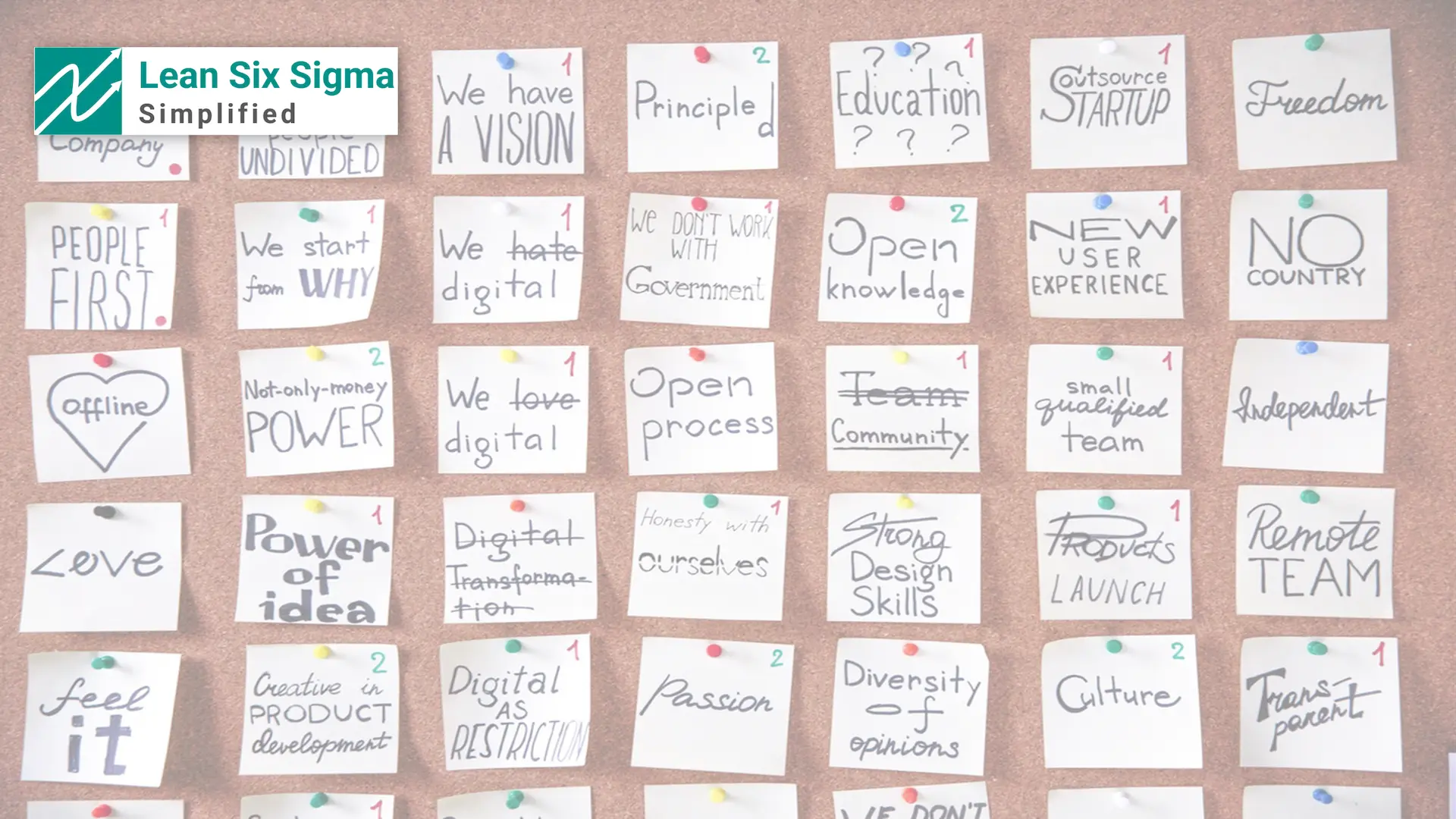
Nominal Group Technique Definition, Examples Steps
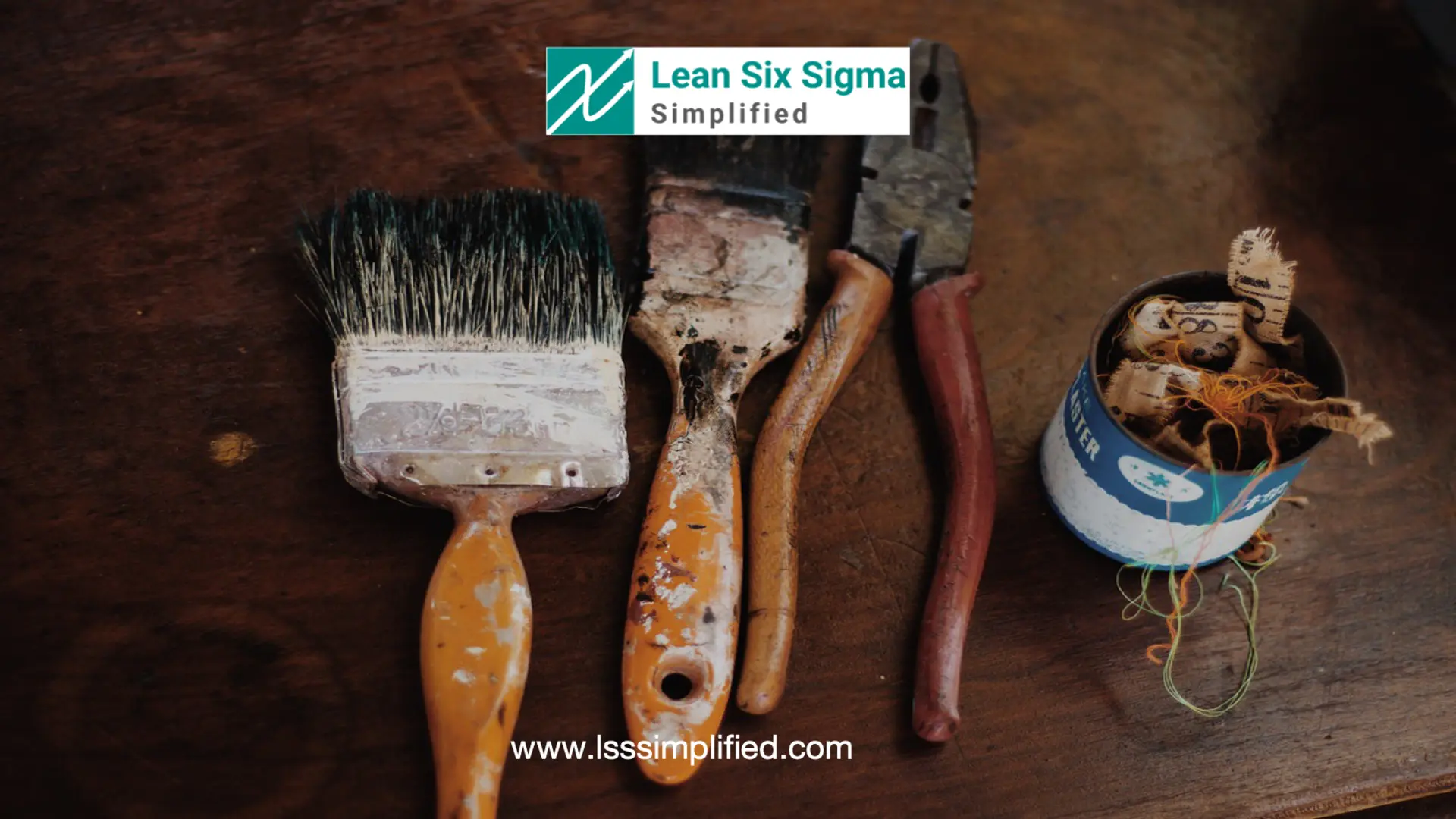
What are the measures of Variation

What are the measures of Central Tendency
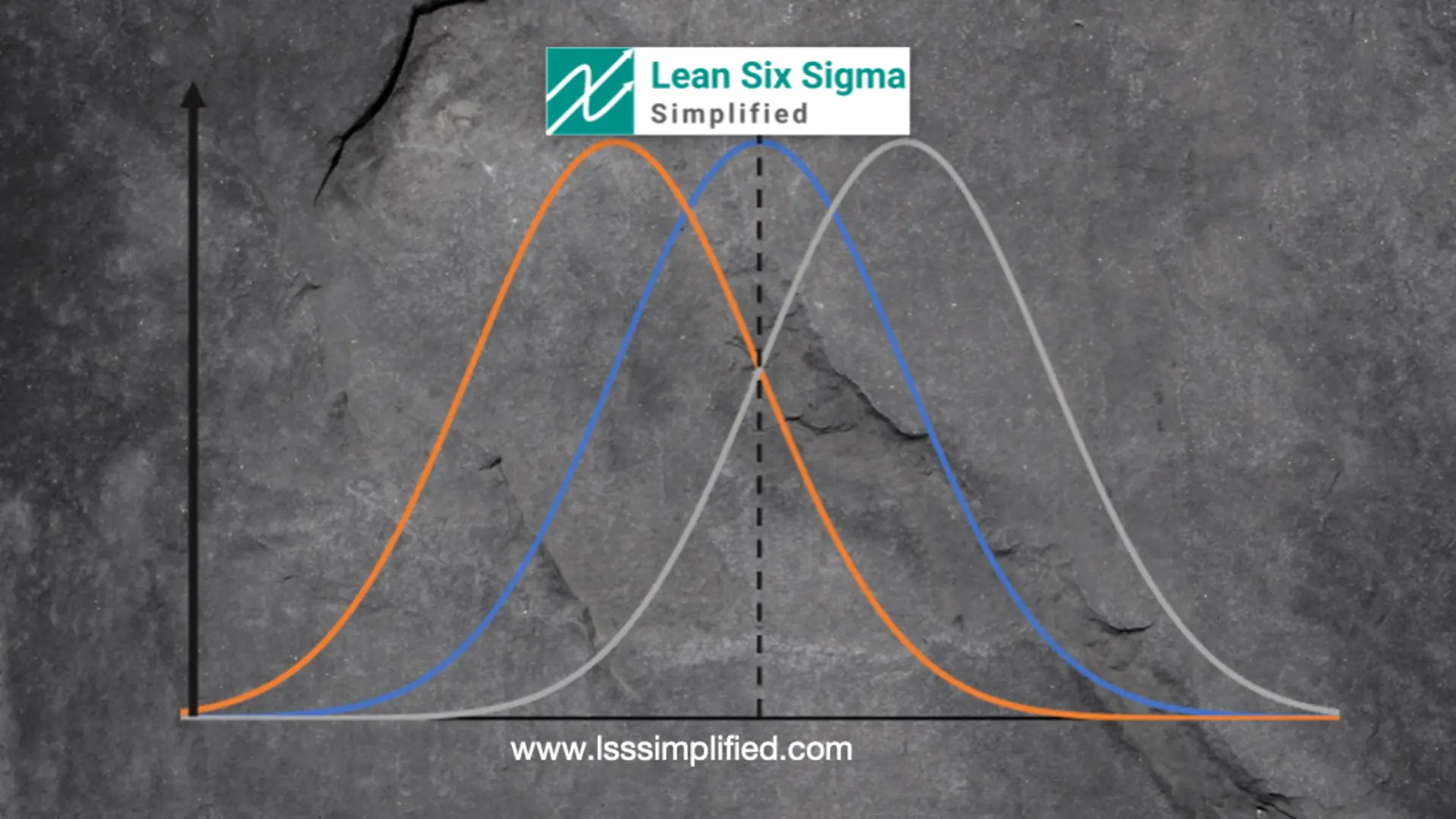
Normal Distribution for Lean Six Sigma

Probability Distribution for Lean Six Sigma
