Lean methodology is a process improvement approach that emphasises the elimination of waste and the maximisation of value in order to improve efficiency and productivity. One of the key concepts in Lean is the identification and elimination of 8 Type of wastes. Initially, these were 7 Type of wastes. The 8th waste was recently added keeping in mind the adoption of Lean methodology in service industry and the current business scenario. These 8 type of wastes are non-value-adding activities that consume resources without providing any benefit to the customer. By identifying and eliminating these wastes, organizations can improve their processes and performance.
8 Type of Wastes
The 8 Type of Wastes in Lean are:
- Overproduction
- Waiting
- Defects
- Excess Inventory
- Motion
- Over processing
- Transport
- Non Utilisation of talent
Please read about the 7 wastes here (opens in a new tab). I will cover the 8th waste in this post.
8th Waste – Non Utilisation of Talent
The 8th waste in Lean methodology is the non-utilisation of talent. This waste refers to the failure to fully utilise the skills and abilities of employees, and to provide them with the necessary training and resources to do their jobs effectively. This waste can manifest itself in several ways, including:
Underutilization of employee skills: When employees are not given tasks or projects that align with their skills and abilities, they are not able to fully contribute to the organization, leading to a lack of engagement and motivation.
Lack of training and development: Without adequate training and development opportunities, employees may not be able to perform their job functions to the best of their abilities.
Inadequate resources: Without access to the right tools and equipment, employees may not be able to perform their job functions as efficiently or effectively as they could.
Limited autonomy: Employees do not have enough autonomy or decision-making power. Such employees may not feel empowered to take ownership of their work and make improvements.
Inefficient communication: Employees are not included in decision-making processes and do not have access to accurate information. Such employees may not be able to fully contribute to problem-solving.
The non-utilization of talent can have a significant impact on the organization’s bottom line. By not fully utilizing the skills and abilities of employees, organizations miss out on potential productivity and efficiency gains. Additionally, a lack of training and development opportunities can lead to high turnover rates, which can be costly.
Ways to eliminate the 8th waste
It’s essential for organizations to identify and eliminate the non-utilisation of talent by providing adequate training, resources and opportunities for the employees to grow and develop. Employees should be given tasks that align with their skills and abilities and provided with the necessary resources and tools to do their job effectively. The management should also allow employees to take ownership of their work and make decisions, and regularly communicate with them to keep them updated on important information. This approach can help organizations to fully utilise the talents and abilities of employees, improve performance and achieve better results.
Master Lean and Six Sigma Acronyms in No Time!
The Ultimate Guide to LSS Lingo – Yours for Free
Subscribe and Get Your Hands on the Most Comprehensive List of 220+ LSS Acronyms Available. No more searching for definitions, no more confusion. Just pure expertise at your fingertips. Get your free guide and other ebooks and templates today. Download Now!
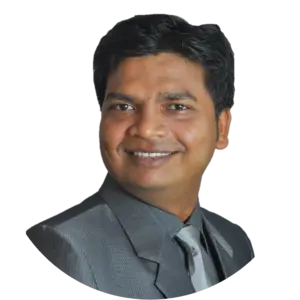
Sachin Naik
Passionate about improving processes and systems | Lean Six Sigma practitioner, trainer and coach for 14+ years consulting giant corporations and fortune 500 companies on Operational Excellence | Start-up enthusiast | Change Management and Design Thinking student | Love to ride and drive
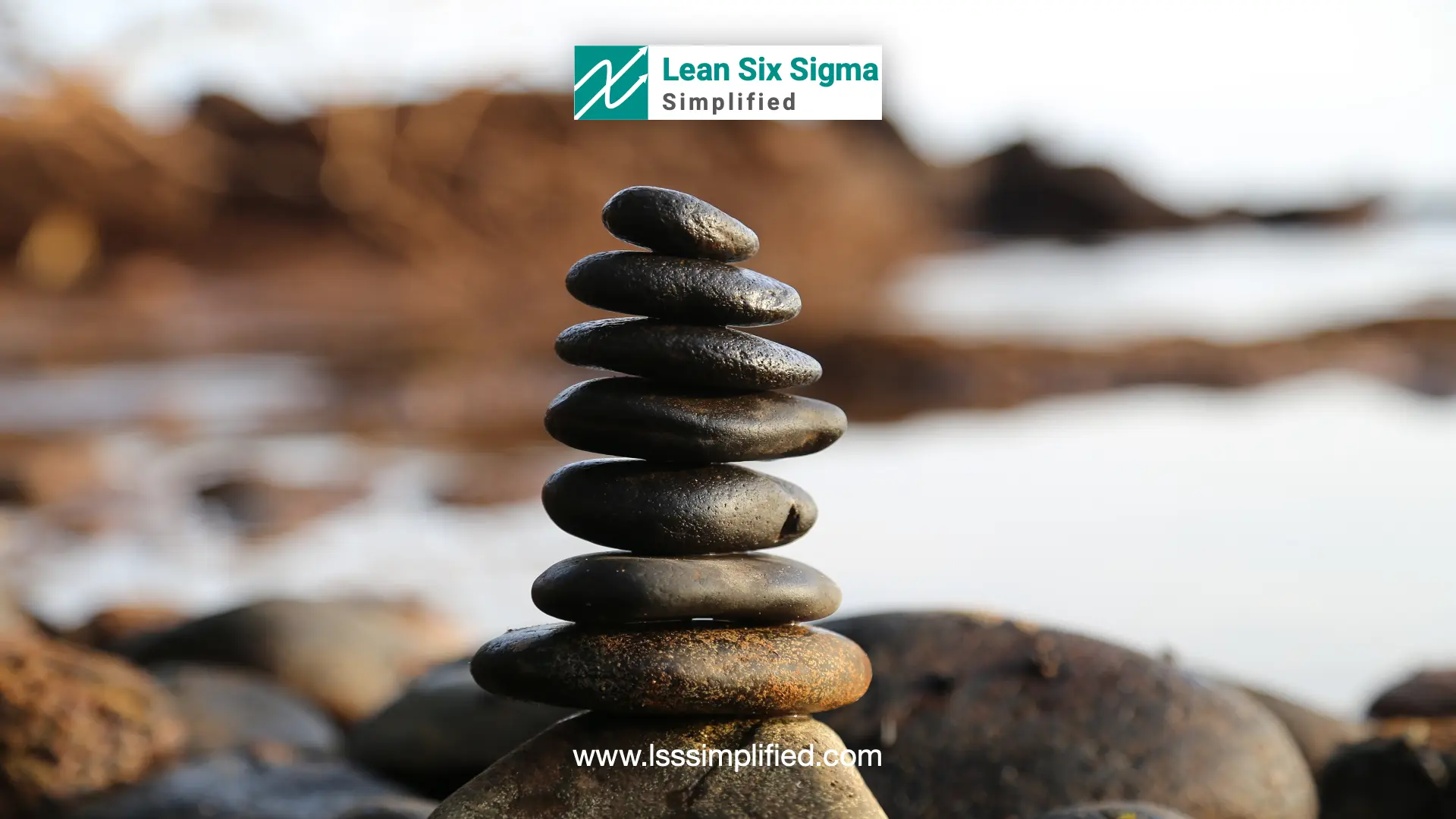
7 Principles of Lean
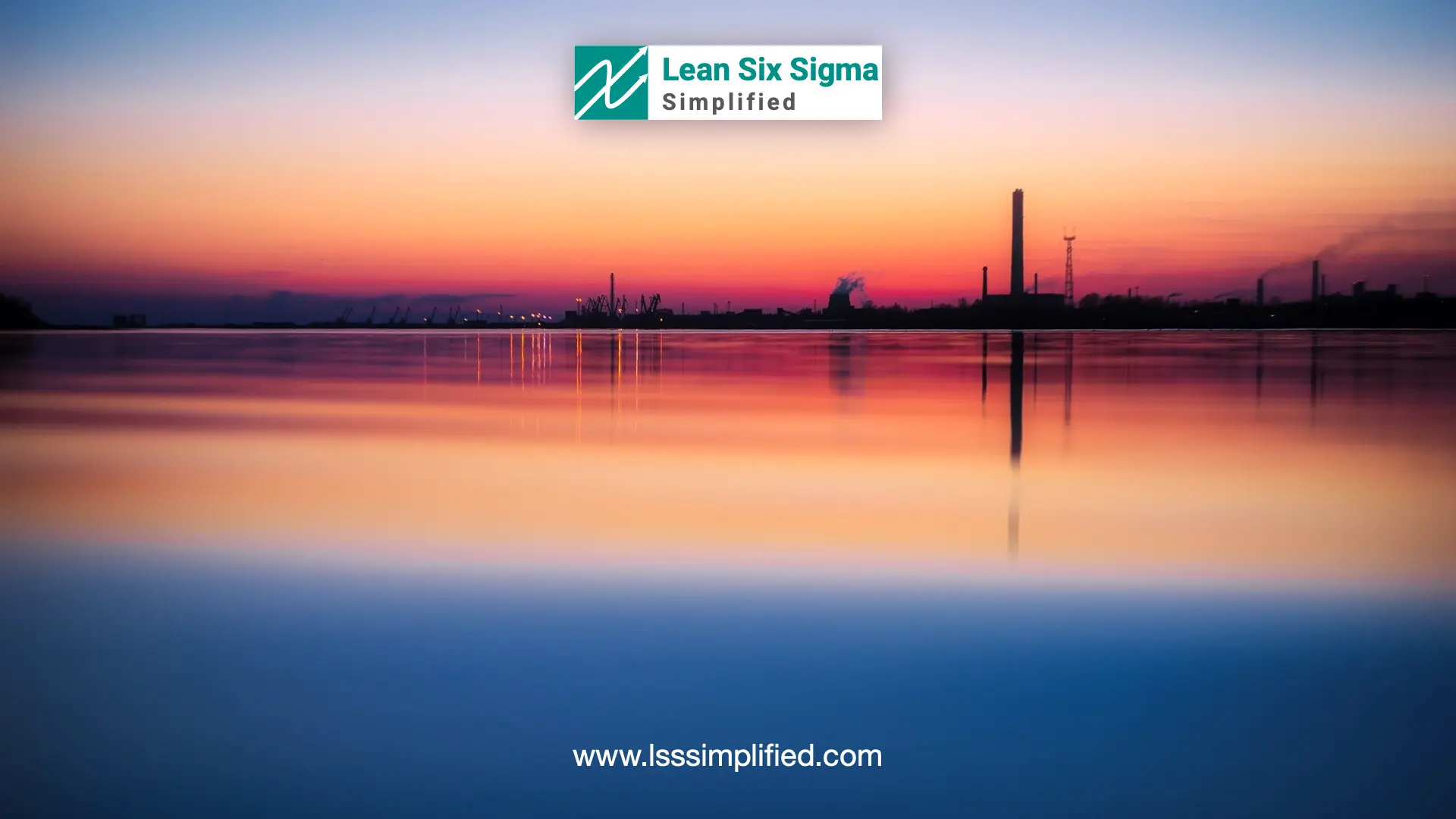
Origin of Lean

Next generation Lean Six Sigma – Harnessing the Power of AI

What is Lean Six Sigma and how it helps your career
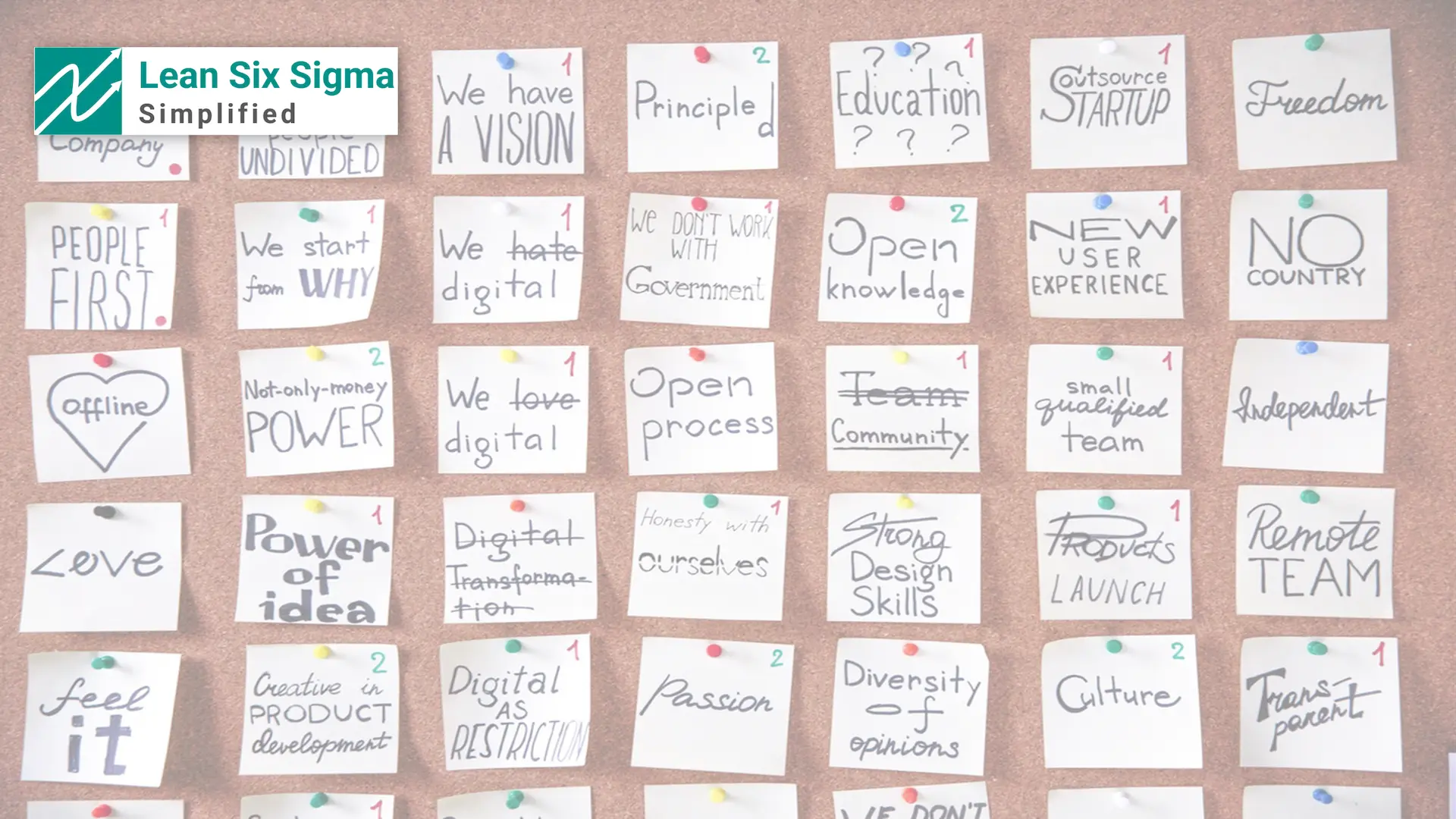
Nominal Group Technique Definition, Examples Steps
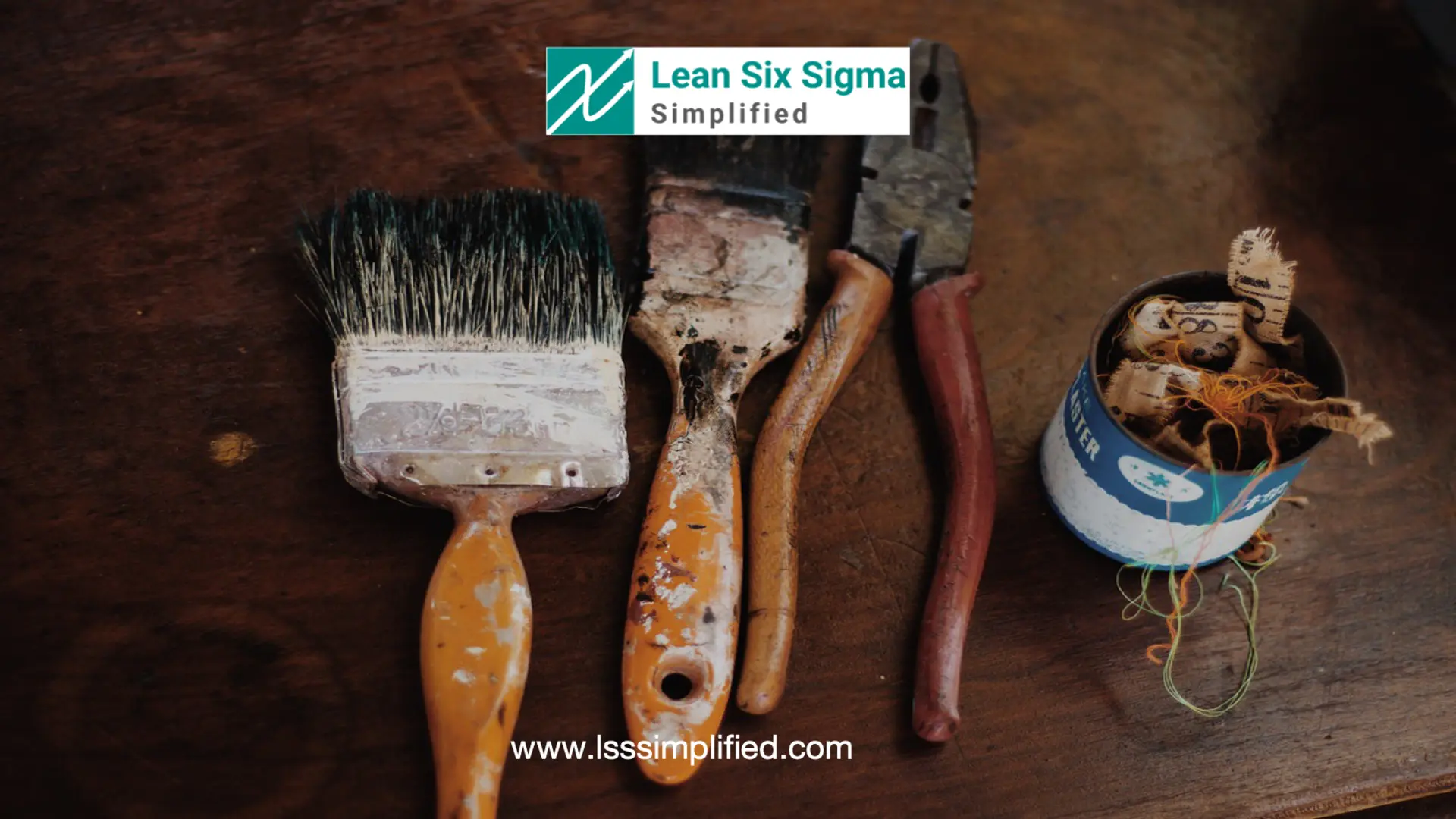
What are the measures of Variation

What are the measures of Central Tendency
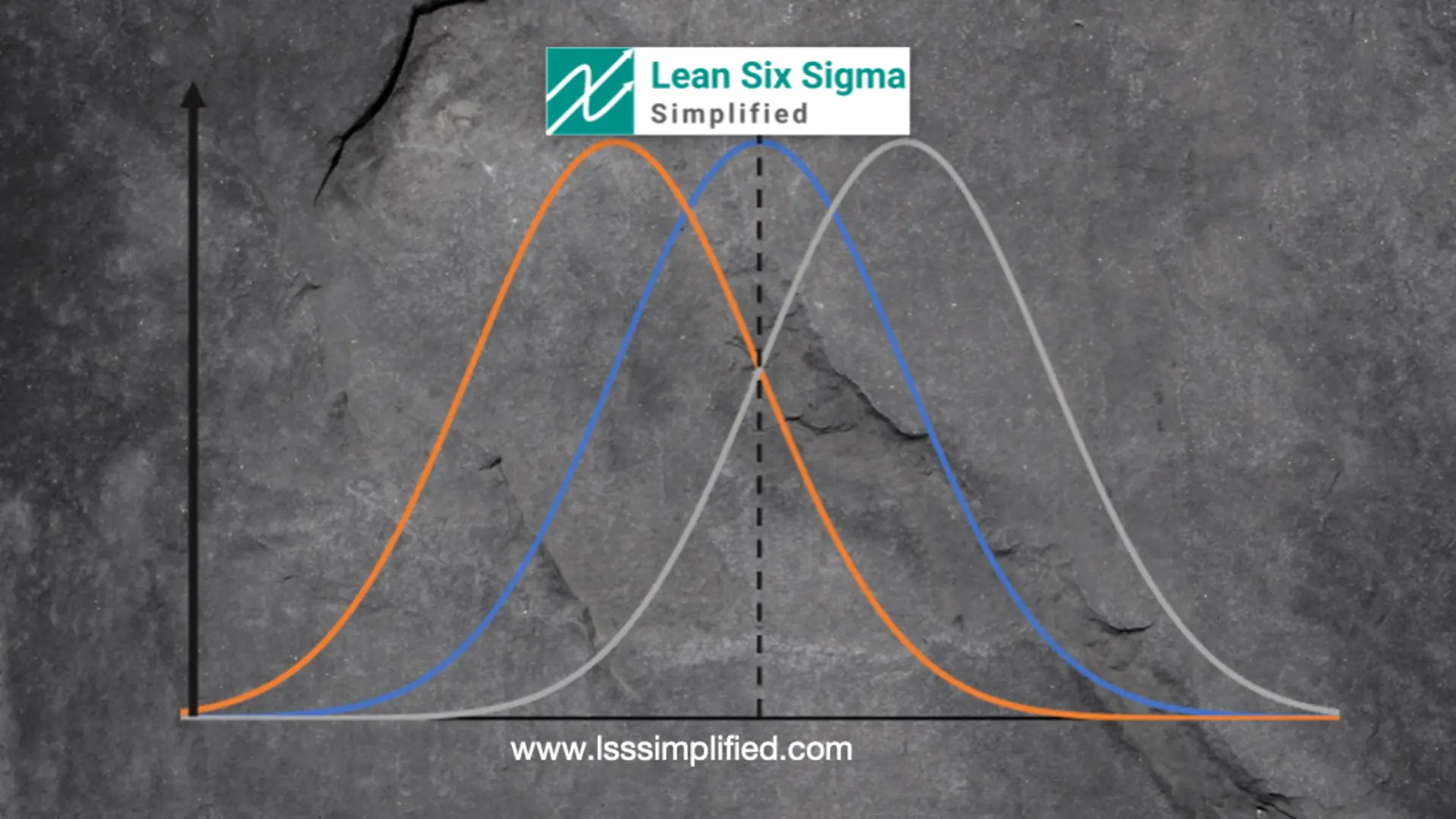
Normal Distribution for Lean Six Sigma

Probability Distribution for Lean Six Sigma
