One key tool used in Lean methodology is the 6M analysis, which looks at six areas of an organization to identify and eliminate sources of waste.
The 6M are:
- Manpower: The number and skills of the people involved in the process
- Methods: The specific procedures used to complete the process
- Machines: The tools and equipment used to complete the process
- Materials: The raw materials used in the process
- Measurement: The methods used to track and evaluate the process
- Mother Nature: The physical environment in which the process takes place.
By analyzing each of these areas, organizations can identify specific sources of waste and inefficiencies, and then take steps to eliminate them.
Meaning of 6M
In the area of manpower, a company might identify that its employees lack the necessary training or skills to effectively complete a particular task. By providing additional training or hiring workers with the necessary skills, the company can improve the efficiency of the process and reduce waste.
In the area of methods, a company might identify that a particular process is unnecessarily complex or time-consuming. By simplifying the process or streamlining certain steps, the company can increase efficiency and reduce waste.
Similarly, in the area of machines, a company might identify that certain tools or equipment are causing delays or breakdowns. By upgrading or replacing these tools or equipment, the company can improve efficiency and reduce waste.
In the area of materials, a company might identify that certain raw materials are causing quality issues or delays. By switching to higher-quality materials or implementing better inventory management practices, the company can improve efficiency and reduce waste.
In the area of measurement, a company might identify that it lacks accurate data on the performance of a particular process. By implementing better tracking and measurement systems, the company can gain a clearer understanding of the process and identify areas for improvement.
Finally, in the area of Mother Nature, a company might identify that the layout of its facility is causing congestion or delays. By rearranging the layout of the facility, the company can improve efficiency and reduce waste.
6M in Fishbone Analysis
Another way to look at 6M is in light of the Fishbone Analysis.
The Fishbone analysis, also known as the Ishikawa diagram or cause-and-effect diagram, is a tool used to identify and analyze the potential causes of a particular problem or issue. One key aspect of the Fishbone analysis is the categorization of potential causes into different groups or “bones” that can be further analysed. One common method of categorizing these causes is the 6M analysis, which looks at six areas or aspects that can contribute to a problem:
- Machine: The equipment or tools used in the process that could be contributing to the problem.
- Material: The raw materials or components used in the process that could be contributing to the problem.
- Method: The procedures, processes, or instructions used in the production process that could be contributing to the problem.
- Manpower: The human factors involved in the process, such as training, communication, or job design. These factors could be contributing to the problem.
- Measurement: The methods and systems used to measure and monitor the process. And detect problems that could be contributing to the problem.
- Mother Nature: The external environment or conditions, such as temperature, humidity, or lighting, that could be contributing to the problem.
Looking at each of these categories allows teams to identify potential causes and helps to organise and structure the problem-solving process.
Application of 6M
A company is experiencing a problem with product defects. A Fishbone analysis using the 6M categories might reveal that a combination of factors are causing the problem. The Machine category might reveal that certain equipment is malfunctioning or is in need of maintenance. The Material category might reveal that certain raw materials are of poor quality. The Method category might reveal that the team is not following certain procedures correctly. The Manpower category might reveal that certain employees lack the necessary training or skills to effectively complete their tasks. The Measurement category might reveal that certain monitoring systems are not working properly. And the Mother Nature category might reveal that certain environmental conditions are causing problems with the process.
Benefits of 6M
Understanding the root causes allows the teams to take necessary actions addressing each cause. This leads to a more efficient and effective problem-solving process.
By using the 6M analysis, organizations can identify and eliminate sources of waste and inefficiencies in a systematic way, which can ultimately lead to increased efficiency and productivity.
The Lean methodology focus on continuous improvement. This means we should not see the 6M analysis as a one-time event. It rather is a regular process that should be repeated over time to identify new sources of waste and inefficiencies as they arise.
Fishbone analysis can be used in a variety of situations to solve different types of problems. The 6M categories can be adjusted or expanded depending on the specific situation or problem at hand. For example, 6M sometimes is also used as 5M1P. In this version, Men is replaces with People to reflect more gender neutrality.
Master Lean and Six Sigma Acronyms in No Time!
The Ultimate Guide to LSS Lingo – Yours for Free
Subscribe and Get Your Hands on the Most Comprehensive List of 220+ LSS Acronyms Available. No more searching for definitions, no more confusion. Just pure expertise at your fingertips. Get your free guide and other ebooks and templates today. Download Now!
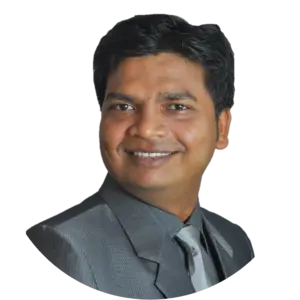
Sachin Naik
Passionate about improving processes and systems | Lean Six Sigma practitioner, trainer and coach for 14+ years consulting giant corporations and fortune 500 companies on Operational Excellence | Start-up enthusiast | Change Management and Design Thinking student | Love to ride and drive
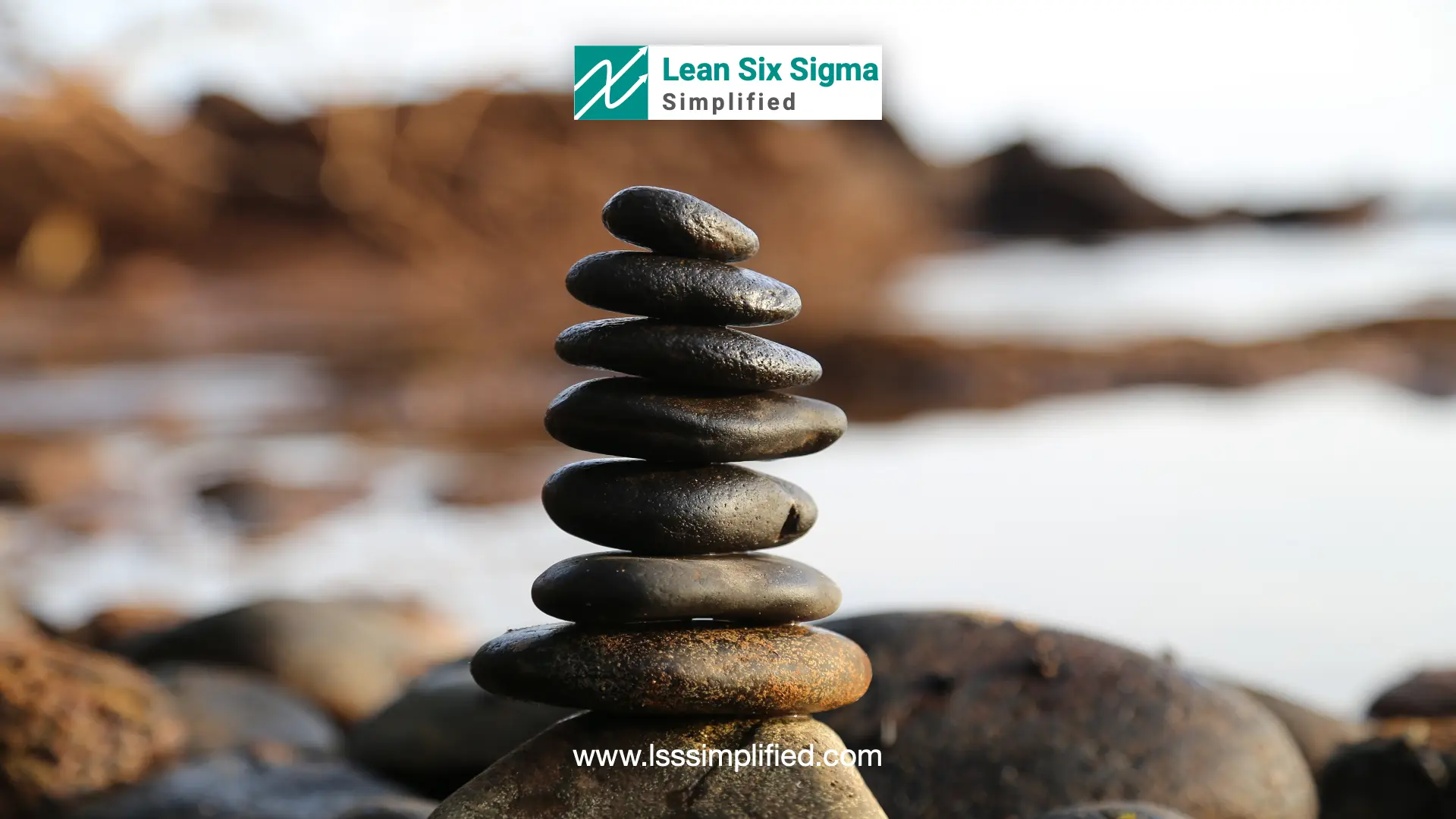
7 Principles of Lean
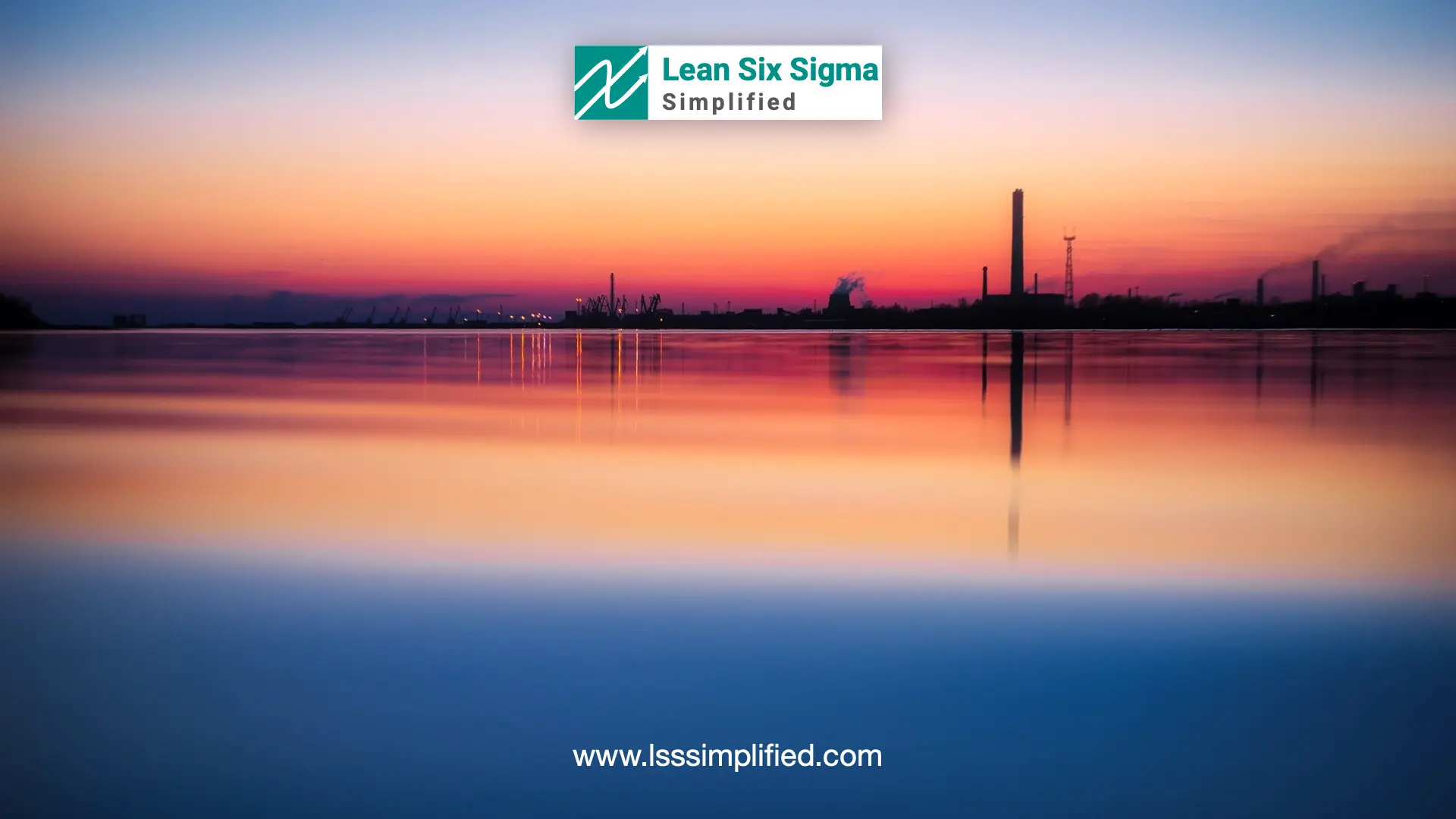
Origin of Lean

Next generation Lean Six Sigma – Harnessing the Power of AI

What is Lean Six Sigma and how it helps your career
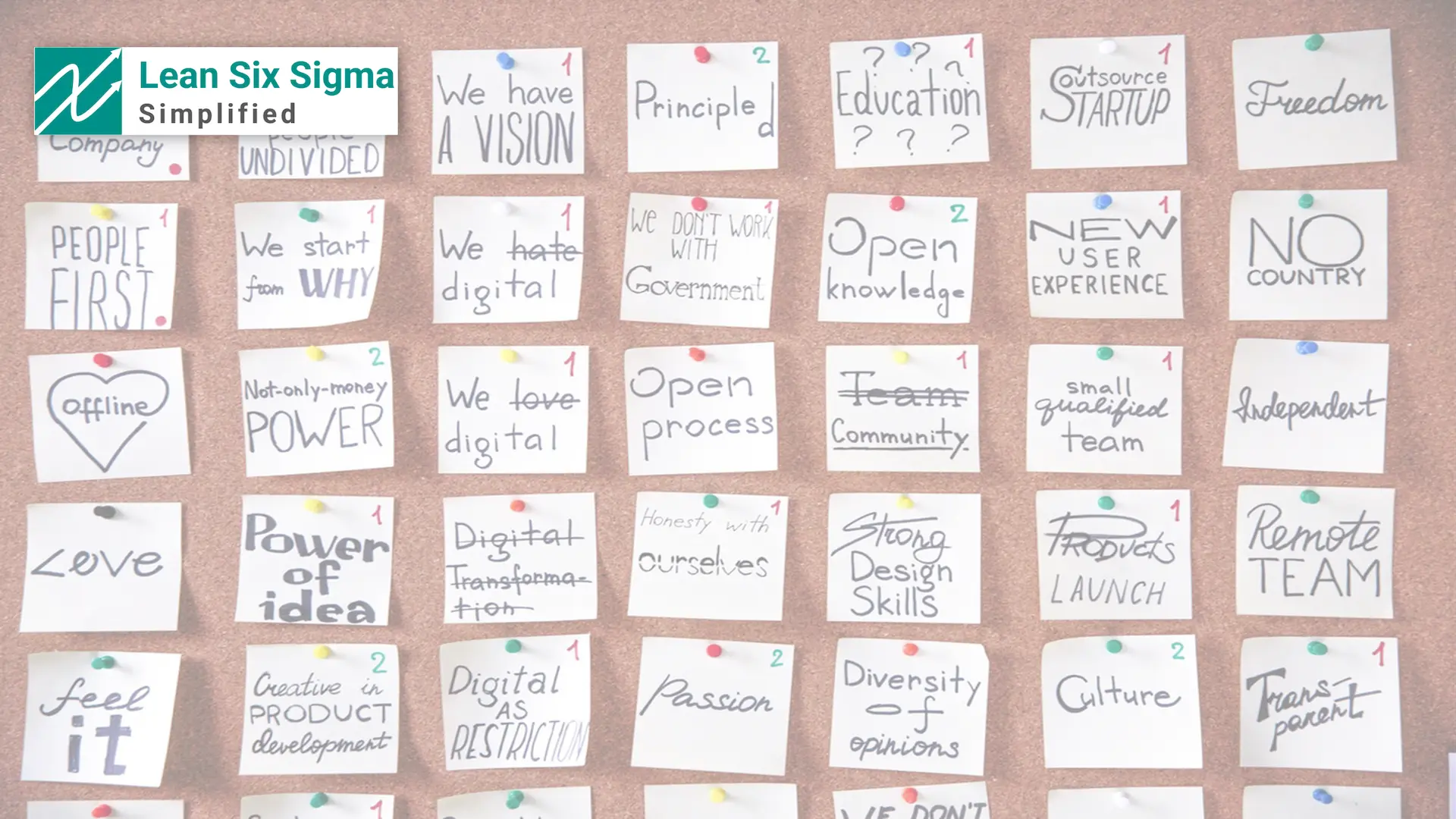
Nominal Group Technique Definition, Examples Steps
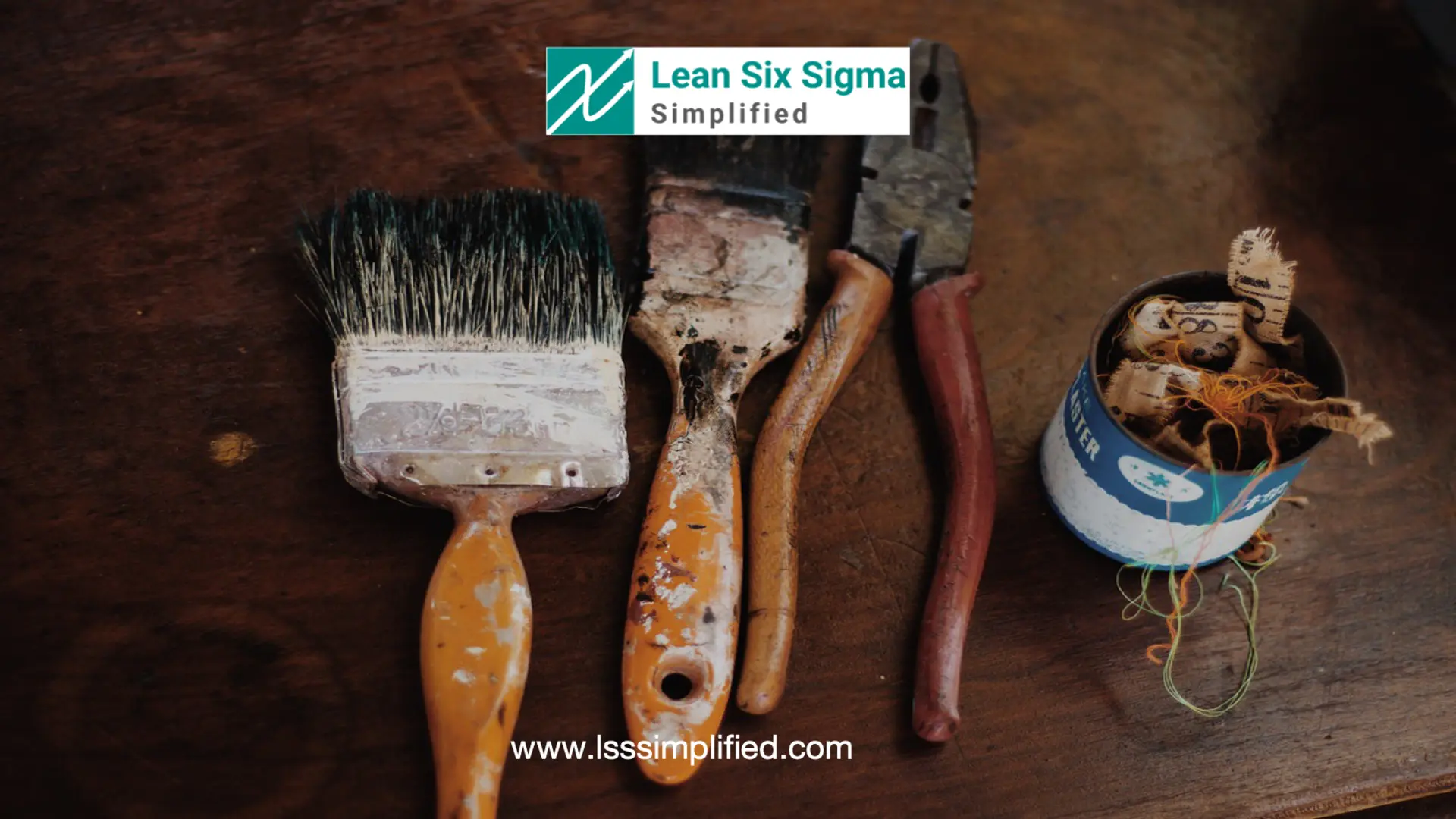
What are the measures of Variation

What are the measures of Central Tendency
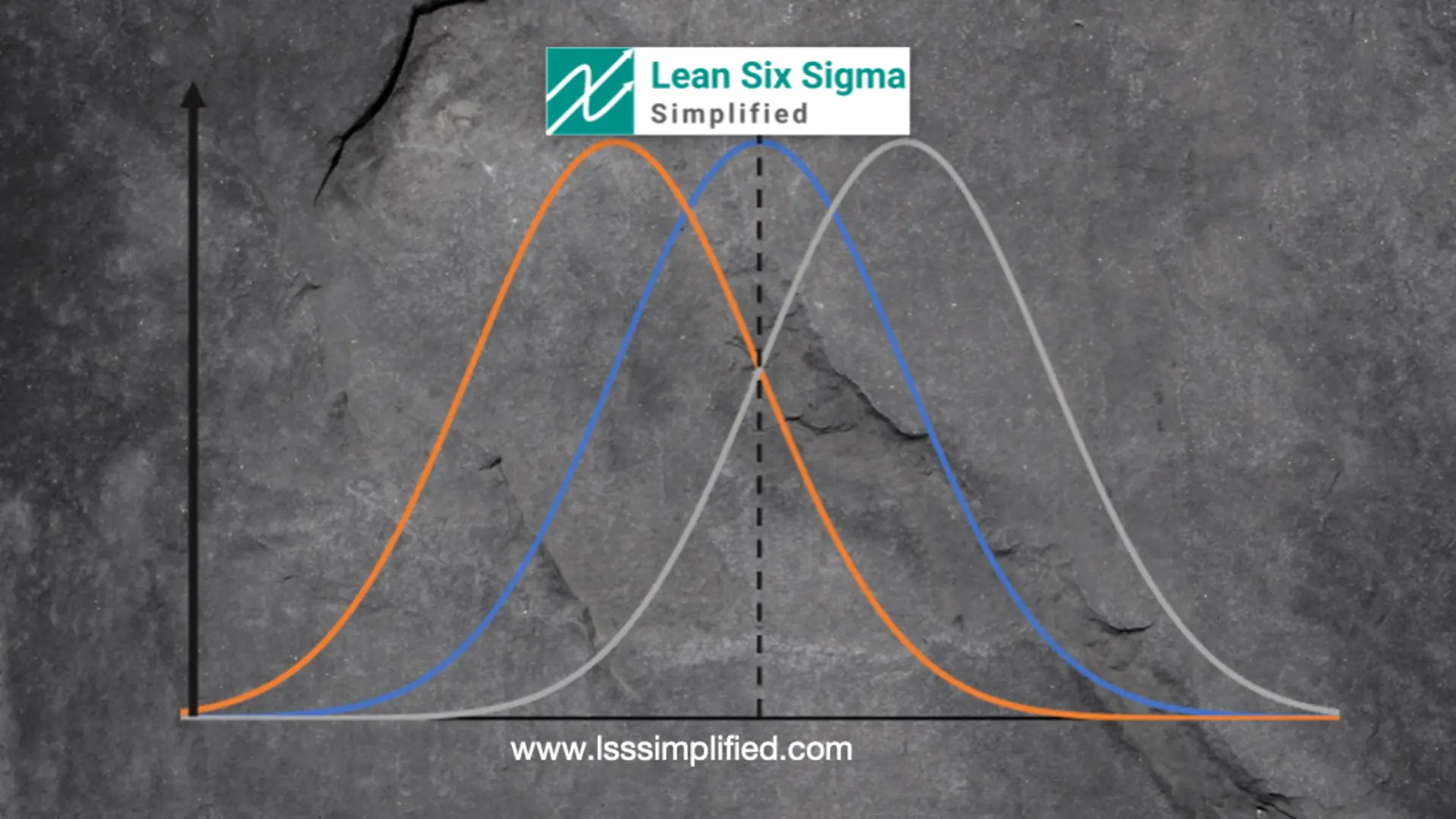
Normal Distribution for Lean Six Sigma

Probability Distribution for Lean Six Sigma
