Andon Line is a manufacturing process control system that helps to monitor and improve production efficiency. It is often used in the automotive industry, but can be applied to any manufacturing process. This system uses visual cues and alarms to alert operators and managers of potential problems on the production line. This allows for quick and efficient problem-solving.
History of Andon Line System
The Andon Line system was first developed by Taiichi Ohno, an industrial engineer at Toyota Motor Corporation, as part of the company’s Lean Manufacturing system. Ohno recognized the need for a system that could quickly alert operators and managers to problems on the production line, allowing for prompt and efficient problem-solving. Toyota implemented this system in the early 1950s. Many other manufacturers had adopted it since then.
How Andon Line System works
The Andon Line system is typically composed of a series of lights or alarms that are placed along the production line. These visual cues are triggered by sensors or other monitoring devices that detect potential problems, such as equipment malfunctions or production delays. The lights or alarms alert operators and managers to the problem, allowing them to quickly investigate and resolve the issue.
Benefits
The Andon Line system offers a number of benefits for manufacturers. It allows for quick and efficient problem-solving, reducing downtime and increasing production efficiency. It also helps to improve communication between operators and managers, allowing for more effective collaboration in solving problems. Additionally, the system can help to identify and eliminate bottlenecks in the production process, leading to overall process improvements.
By the way, do check out the Certified Lean Six Sigma Black Belt Handbook – it is one of the most essential guide for anyone trying to get certified as LSS Black belt or in general wants to understand LSS and improve processes. – check it out here.
Implementation of Andon Line System
Implementing an Andon Line system can be a complex process, requiring careful planning and coordination. It typically involves selecting and installing the appropriate monitoring devices and alarms, as well as training operators and managers on how to use the system. It is also important to establish clear procedures for responding to alarms and resolving problems.
The Andon Line system is an effective tool for monitoring and improving production efficiency. By quickly alerting operators and managers to potential problems, it allows for prompt and efficient problem-solving, reducing downtime and increasing production efficiency. While implementation can be complex, the benefits of the Andon Line system make it a valuable addition to any manufacturing process.
Master Lean and Six Sigma Acronyms in No Time!
The Ultimate Guide to LSS Lingo – Yours for Free
Subscribe and Get Your Hands on the Most Comprehensive List of 220+ LSS Acronyms Available. No more searching for definitions, no more confusion. Just pure expertise at your fingertips. Get your free guide and other ebooks and templates today. Download Now!
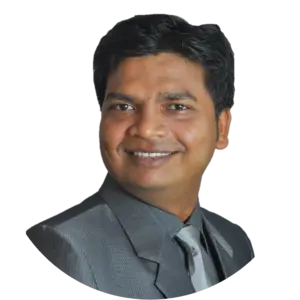
Sachin Naik
Passionate about improving processes and systems | Lean Six Sigma practitioner, trainer and coach for 14+ years consulting giant corporations and fortune 500 companies on Operational Excellence | Start-up enthusiast | Change Management and Design Thinking student | Love to ride and drive
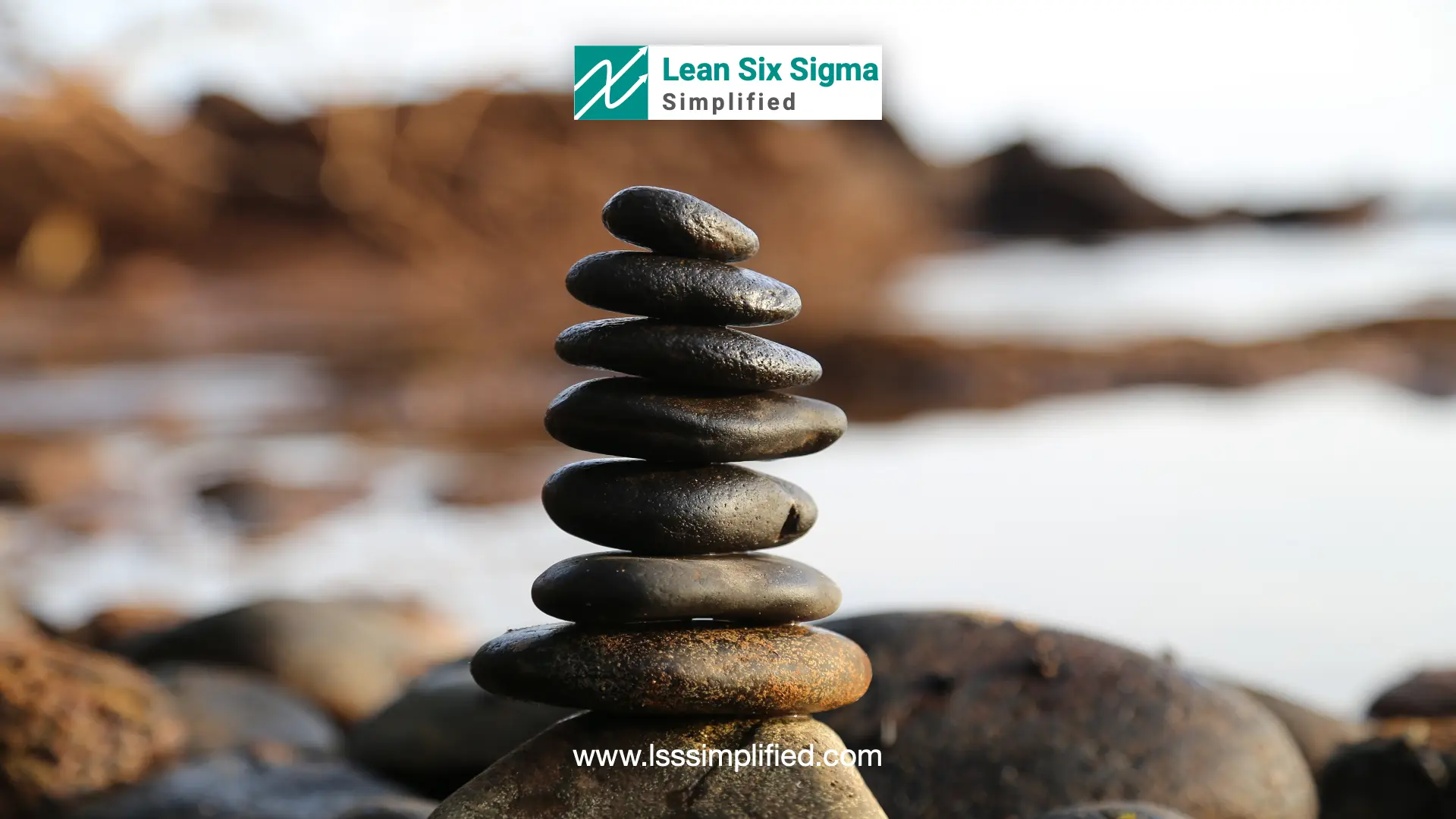
7 Principles of Lean
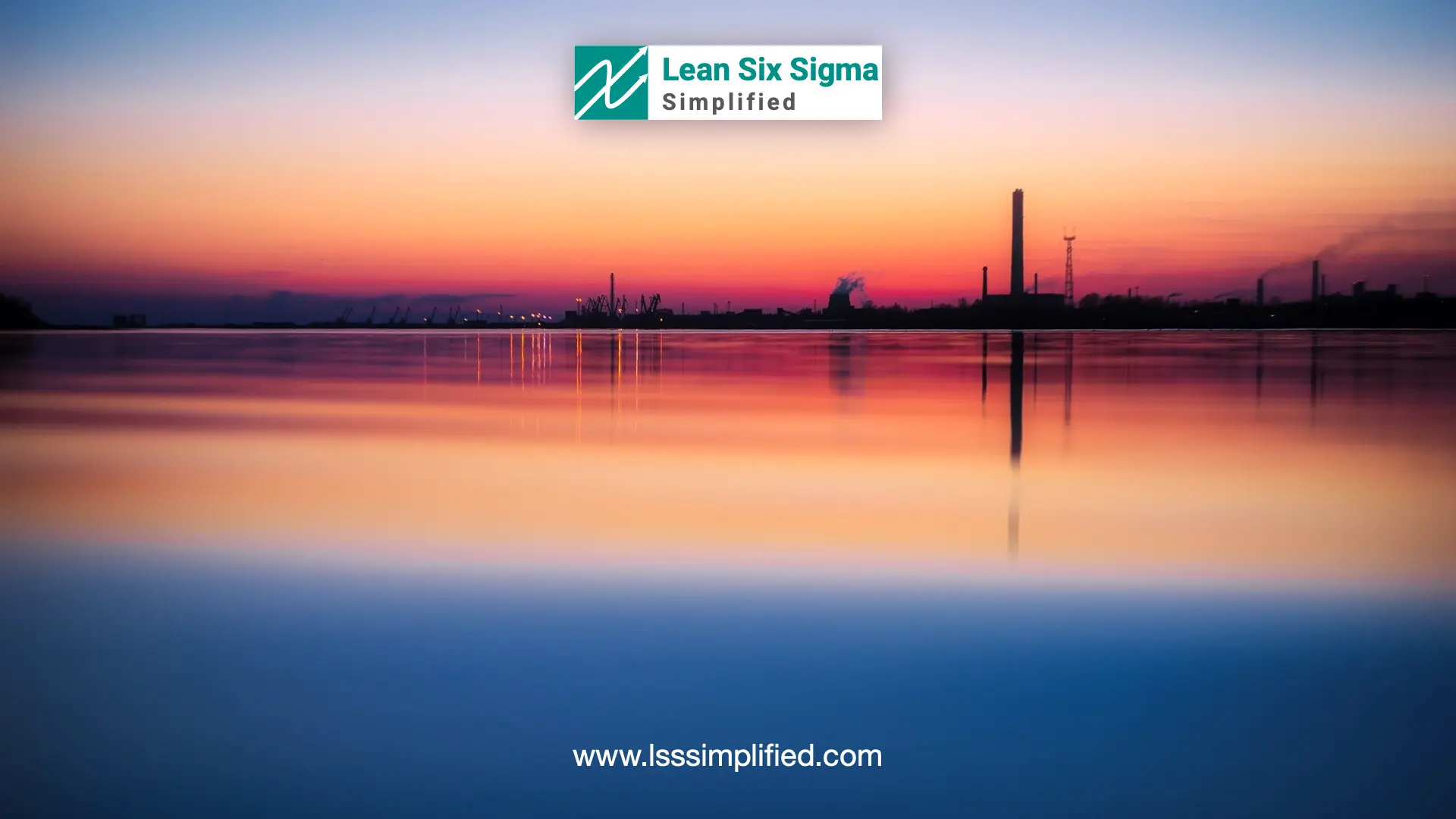
Origin of Lean

Next generation Lean Six Sigma – Harnessing the Power of AI

What is Lean Six Sigma and how it helps your career
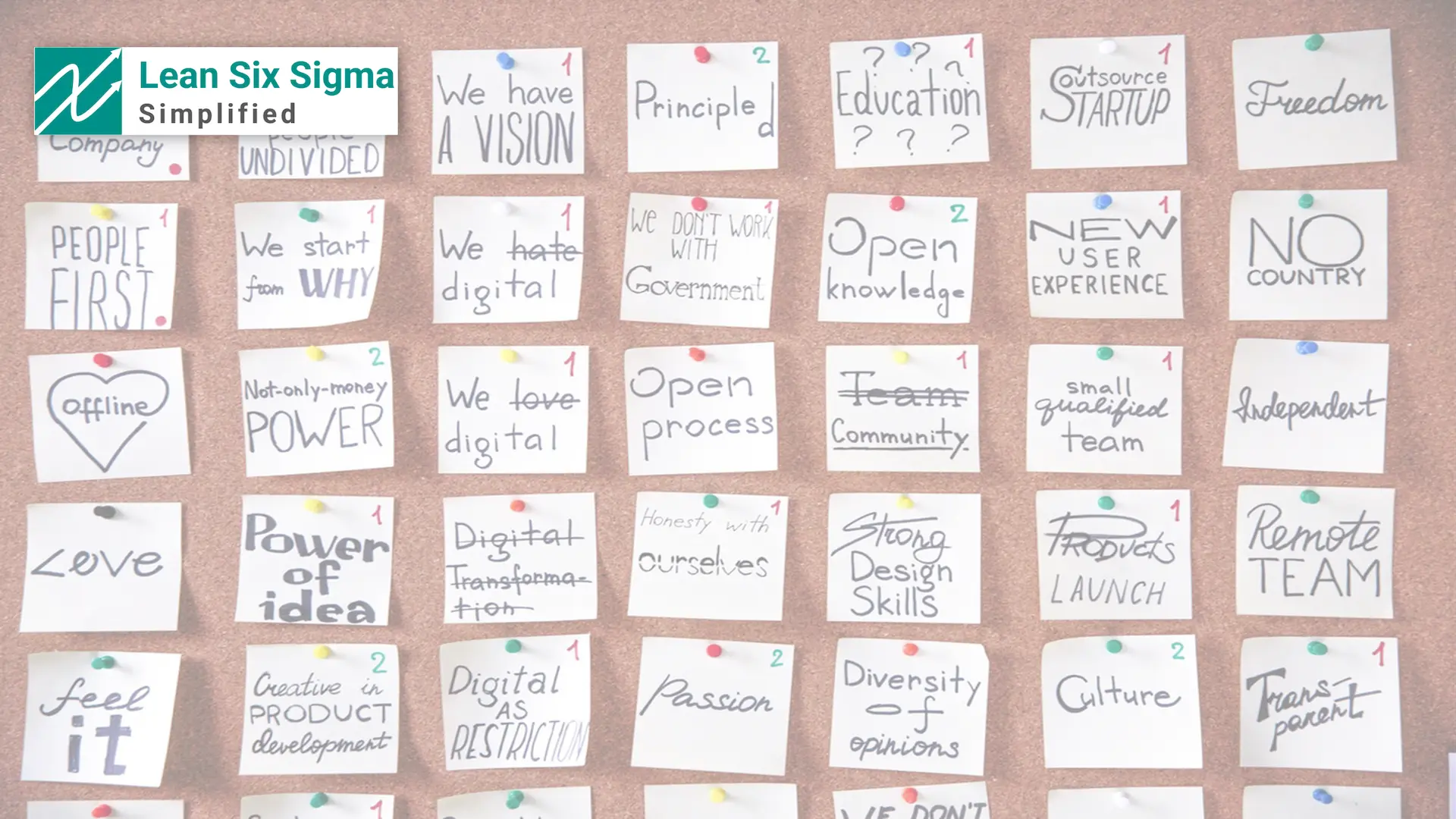
Nominal Group Technique Definition, Examples Steps
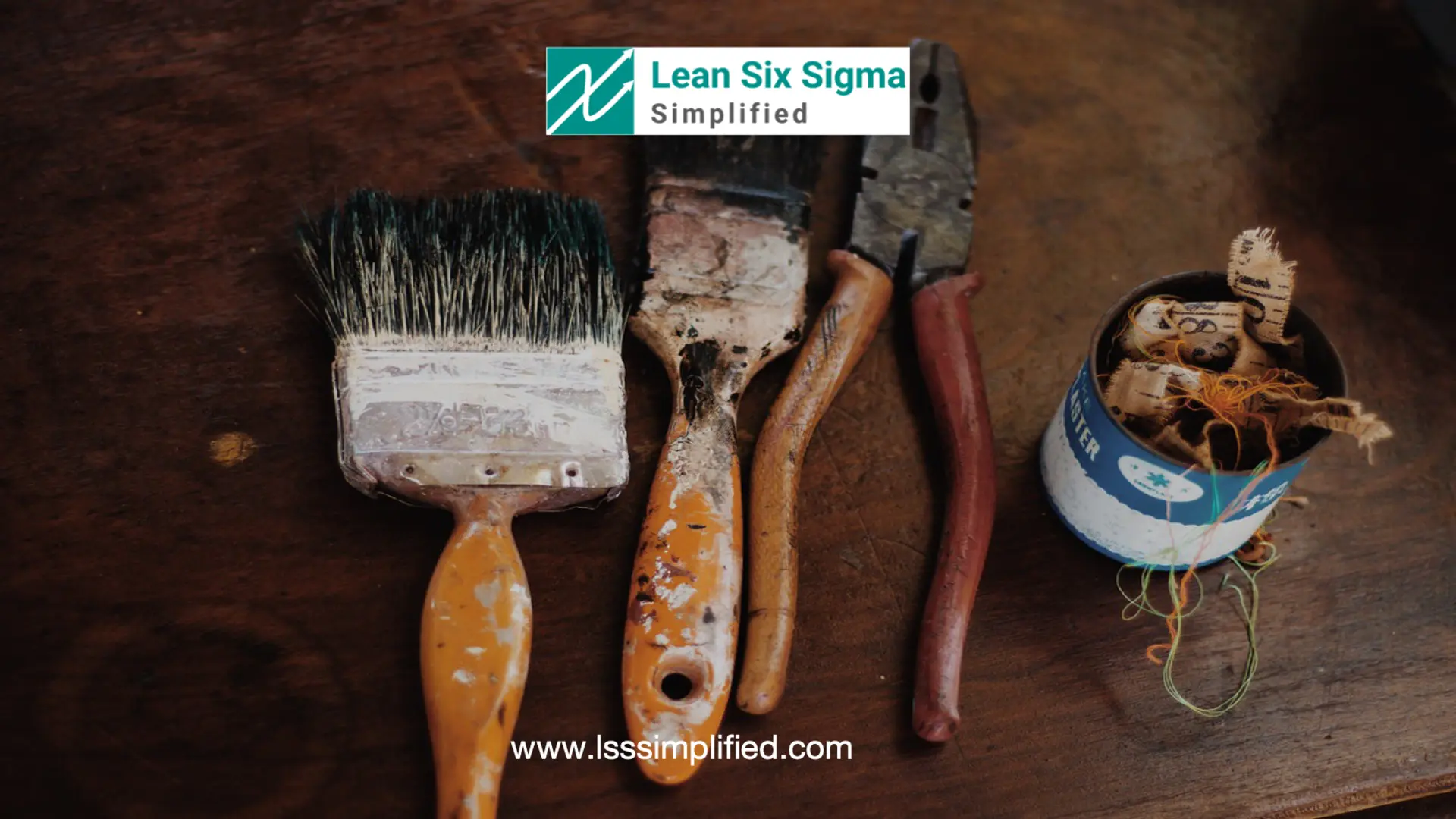
What are the measures of Variation

What are the measures of Central Tendency
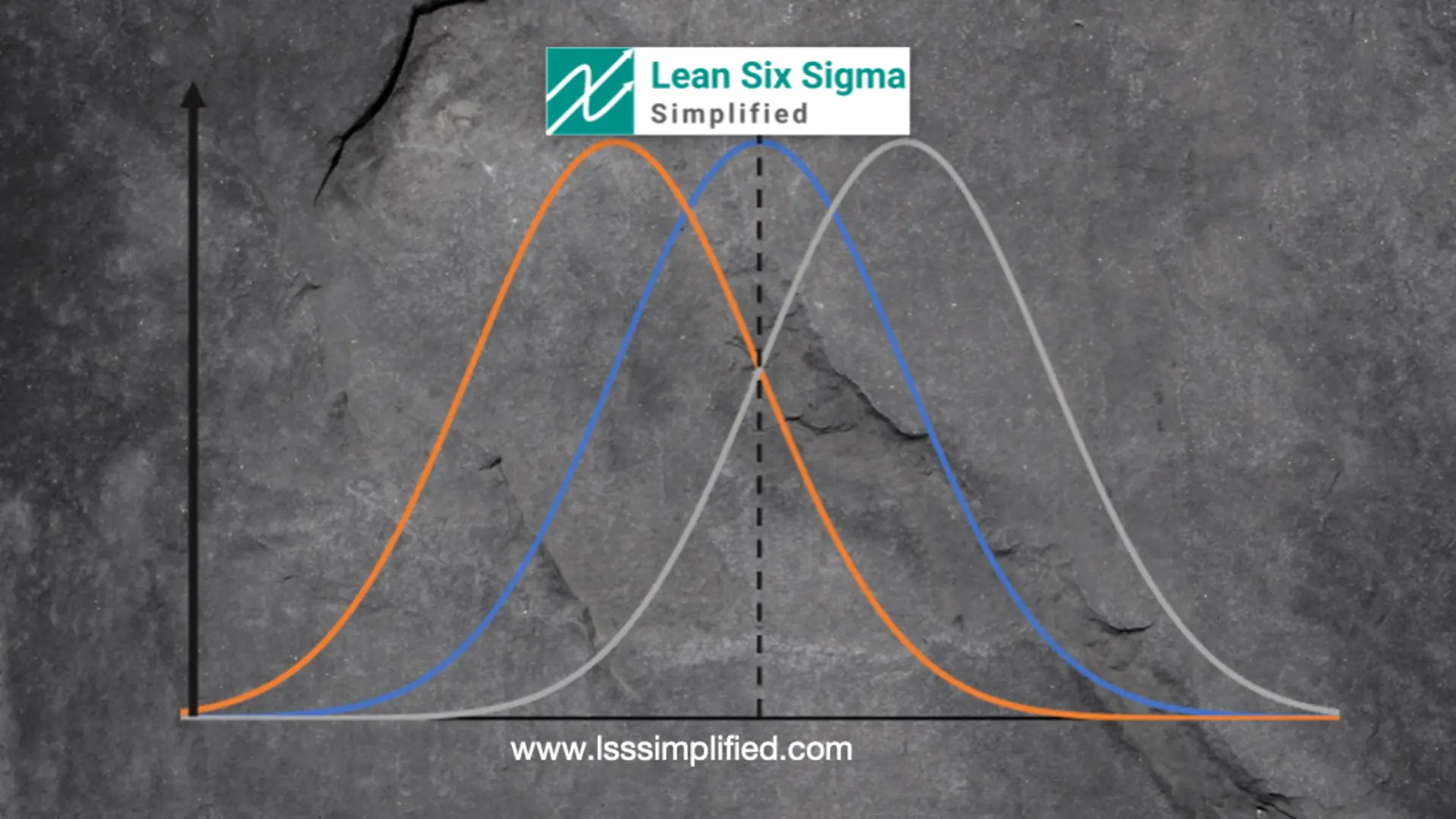
Normal Distribution for Lean Six Sigma

Probability Distribution for Lean Six Sigma
