Manufacturing systems have undergone significant changes in recent years, with the introduction of new technologies and the increasing demand for flexibility and adaptability. An adaptable manufacturing system is a type of manufacturing system that can quickly and easily adapt to changing production requirements, such as changes in product design or production volume. This article will explore the concept of adaptable manufacturing systems, including their benefits, challenges, and current trends in the field.
Benefits of Adaptable Manufacturing System
There are several benefits of adaptable manufacturing system, including:
- Increased efficiency: Adaptable manufacturing system can quickly and easily adapt to changing production requirements, reducing downtime and increasing overall efficiency.
- Reduced costs: Adaptable manufacturing system can reduce costs by minimising the need for specialised equipment. And also by reducing the need for retooling and reconfiguration.
- Improved product quality: Adaptable manufacturing systems can improve product quality by allowing for quick and easy adjustments to production processes.
- Increased flexibility: Adaptable manufacturing systems can increase flexibility of a manufacturing unit. It does this by allowing for the production of a wide range of products with minimal changes to the process.
Challenges of Adaptable Manufacturing System
While adaptable manufacturing system offer many benefits, there are also challenges associated with implementing and maintaining them. These challenges include:
- High initial costs: The costs associated with implementing an adaptable manufacturing system can be high. This makes it difficult for small and medium-sized enterprises to invest in them.
- Complexity: Adaptable manufacturing system can be complex and difficult to understand, making it difficult for operators to use them effectively.
- Maintenance: Adaptable manufacturing systems require regular maintenance and calibration, which can be time-consuming and costly.
- Integration with existing systems: Adaptable manufacturing systems may require significant changes to existing systems and processes, which can be difficult to implement.
Current Trends in Adaptable Manufacturing Systems
Several trends are currently driving the development of adaptable manufacturing system, including:
- Industry 4.0: The fourth industrial revolution, commonly known as Industry 4.0, is driving the development of adaptable manufacturing systems through the use of new technologies such as the Internet of Things (IoT), artificial intelligence (AI), and cyber-physical systems.
- Additive manufacturing: Additive manufacturing, also known as 3D printing, is becoming increasingly popular in the manufacturing industry, and is driving the development of adaptable manufacturing system that can quickly and easily adapt to changing production requirements.
- Sustainable manufacturing: The push towards sustainable manufacturing is driving the development of adaptable manufacturing systems that can reduce waste and minimise the use of resources.
By the way, do check out the Certified Lean Six Sigma Black Belt Handbook – it is one of the most essential guide for anyone trying to get certified as LSS Black belt or in general wants to understand LSS and improve processes. – check it out here.
Example of Adaptable Manufacturing System (AMS)
A car manufacturing company, producing various models of cars, realised the need for flexibility and responsiveness to changing production requirements. They invested in an Adaptable Manufacturing System (AMS) to improve efficiency and reduce costs. The company implemented a system with flexible production cells, where machines and equipment could be quickly reconfigured to suit different production processes. This allowed for quick and easy switching between different models of cars and faster production ramp-up and ramp-down.
The company also invested in advanced automation technology, such as robots and AI systems, which helped to improve efficiency and reduce costs. The robots were programmed to perform multiple tasks such as welding and painting and easily switch between them. Additionally, the company implemented a real-time data collection and analysis system to improve their decision-making process by providing real-time information on production processes, resource utilization, and equipment performance.
The implementation of AMS allowed the company to be highly flexible and responsive to changing market conditions, enabling them to quickly adapt to changes in customer demand and production requirements, which improved their competitiveness and profitability.
Conclusion
Adaptable manufacturing systems offer many benefits, including increased efficiency, reduced costs, improved product quality, and increased flexibility. However, there are also challenges associated with implementing and maintaining these systems. Current trends in the field, such as Industry 4.0, additive manufacturing, and sustainable manufacturing, are driving the development of adaptable manufacturing systems. Overall, adaptable manufacturing systems are an important area of manufacturing technology that is likely to continue to grow in importance in the coming years.
Master Lean and Six Sigma Acronyms in No Time!
The Ultimate Guide to LSS Lingo – Yours for Free
Subscribe and Get Your Hands on the Most Comprehensive List of 220+ LSS Acronyms Available. No more searching for definitions, no more confusion. Just pure expertise at your fingertips. Get your free guide and other ebooks and templates today. Download Now!
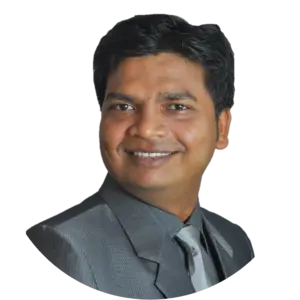
Sachin Naik
Passionate about improving processes and systems | Lean Six Sigma practitioner, trainer and coach for 14+ years consulting giant corporations and fortune 500 companies on Operational Excellence | Start-up enthusiast | Change Management and Design Thinking student | Love to ride and drive
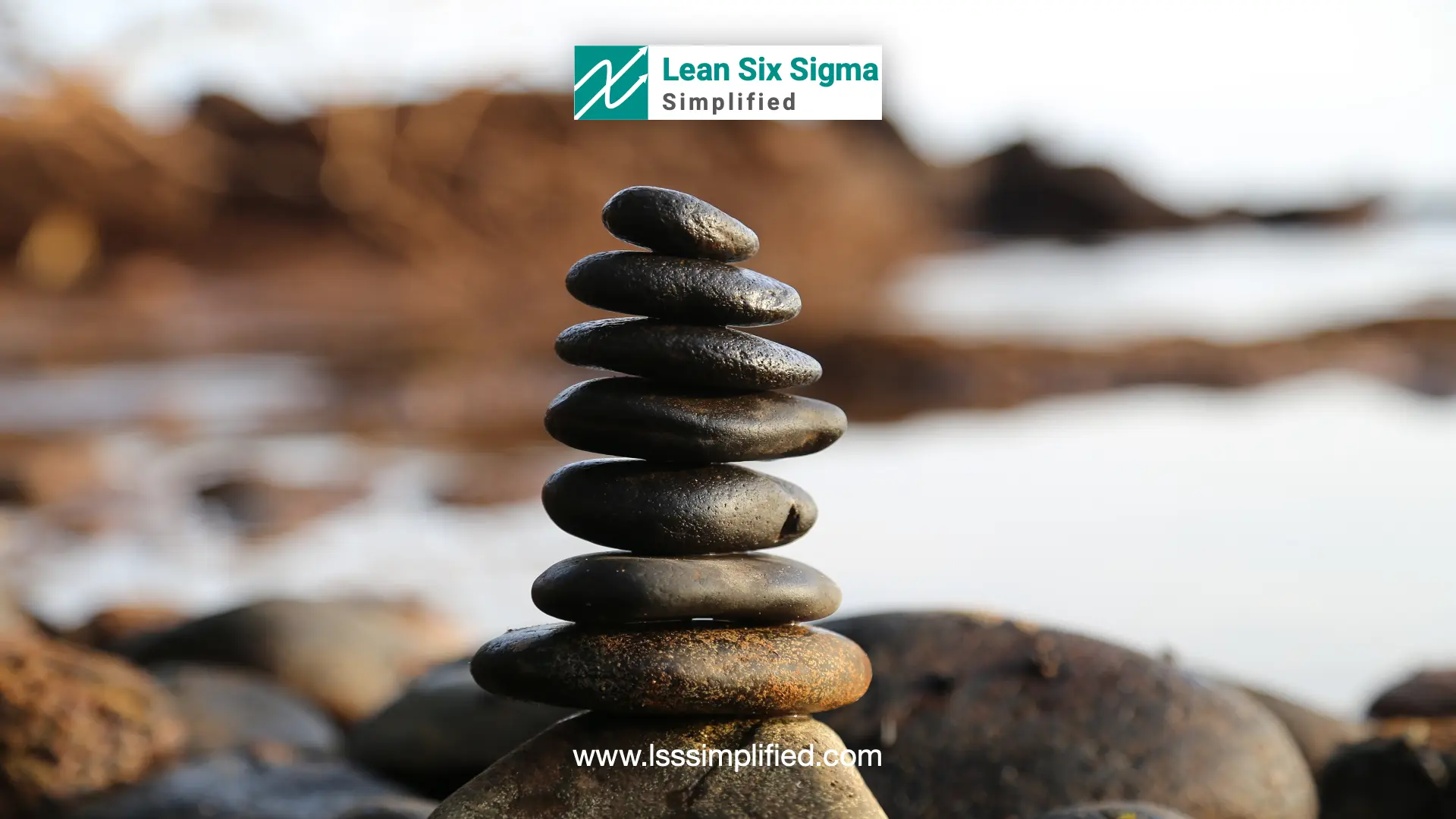
7 Principles of Lean
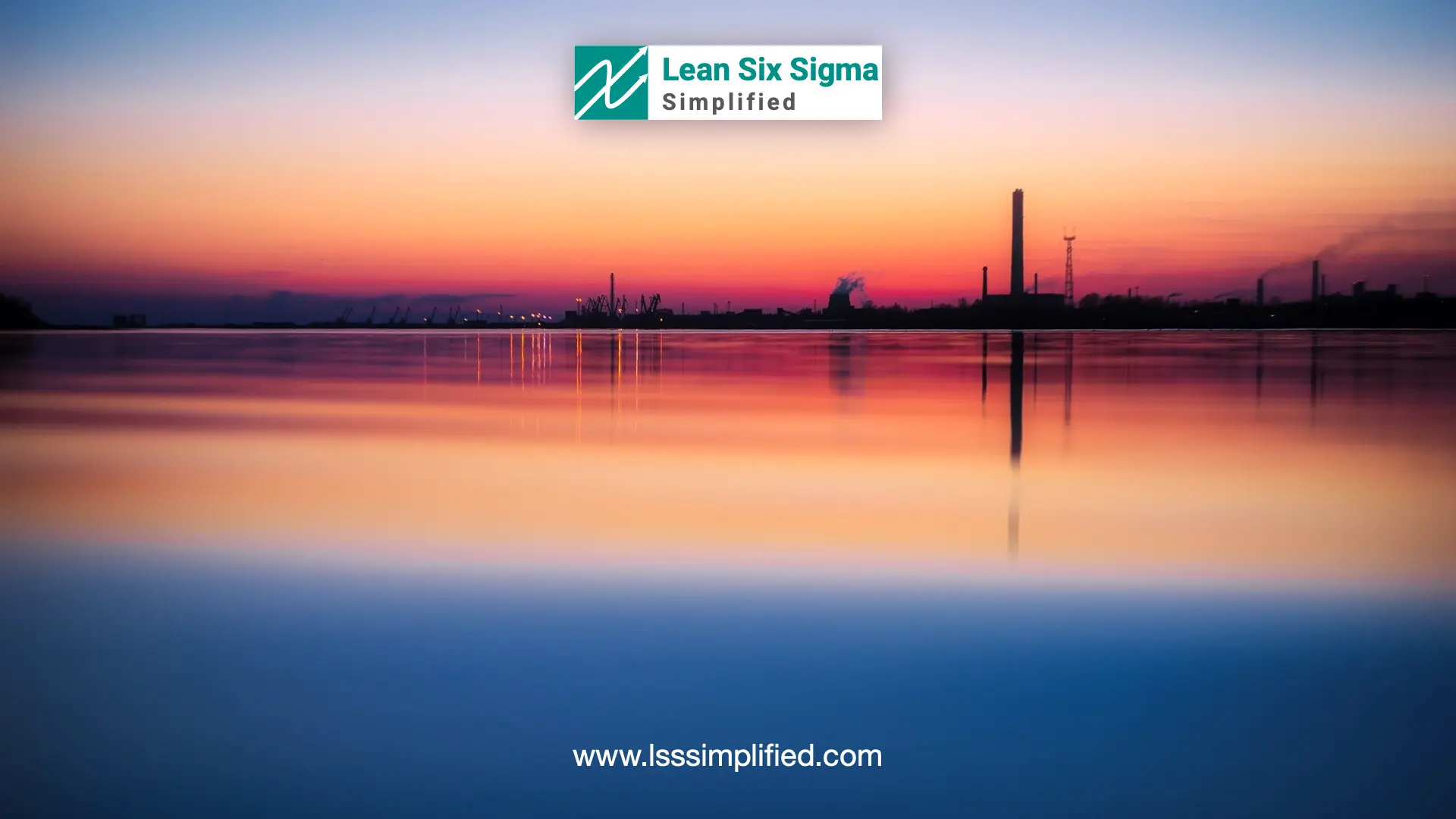
Origin of Lean

Next generation Lean Six Sigma – Harnessing the Power of AI

What is Lean Six Sigma and how it helps your career
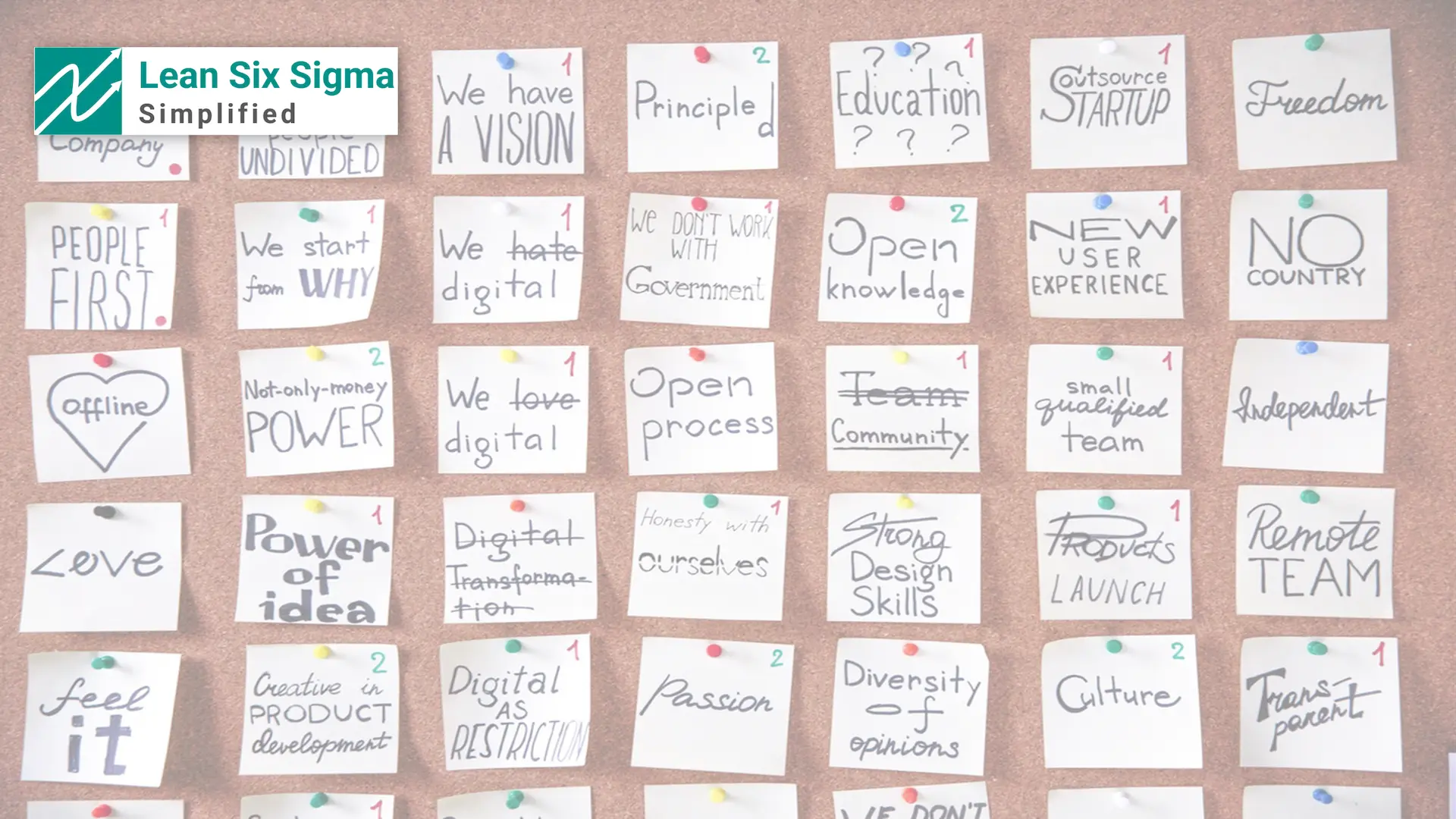
Nominal Group Technique Definition, Examples Steps
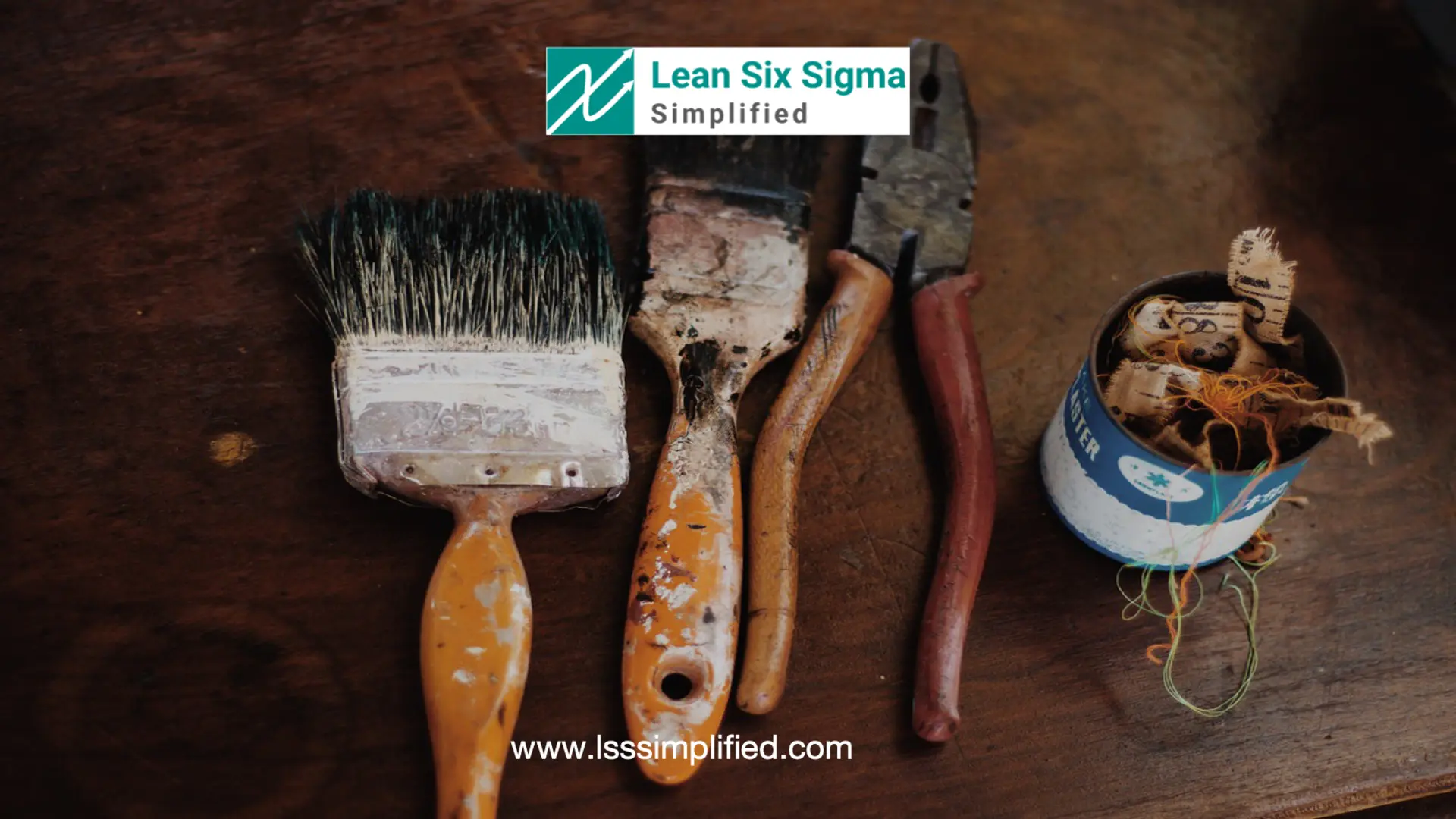
What are the measures of Variation

What are the measures of Central Tendency
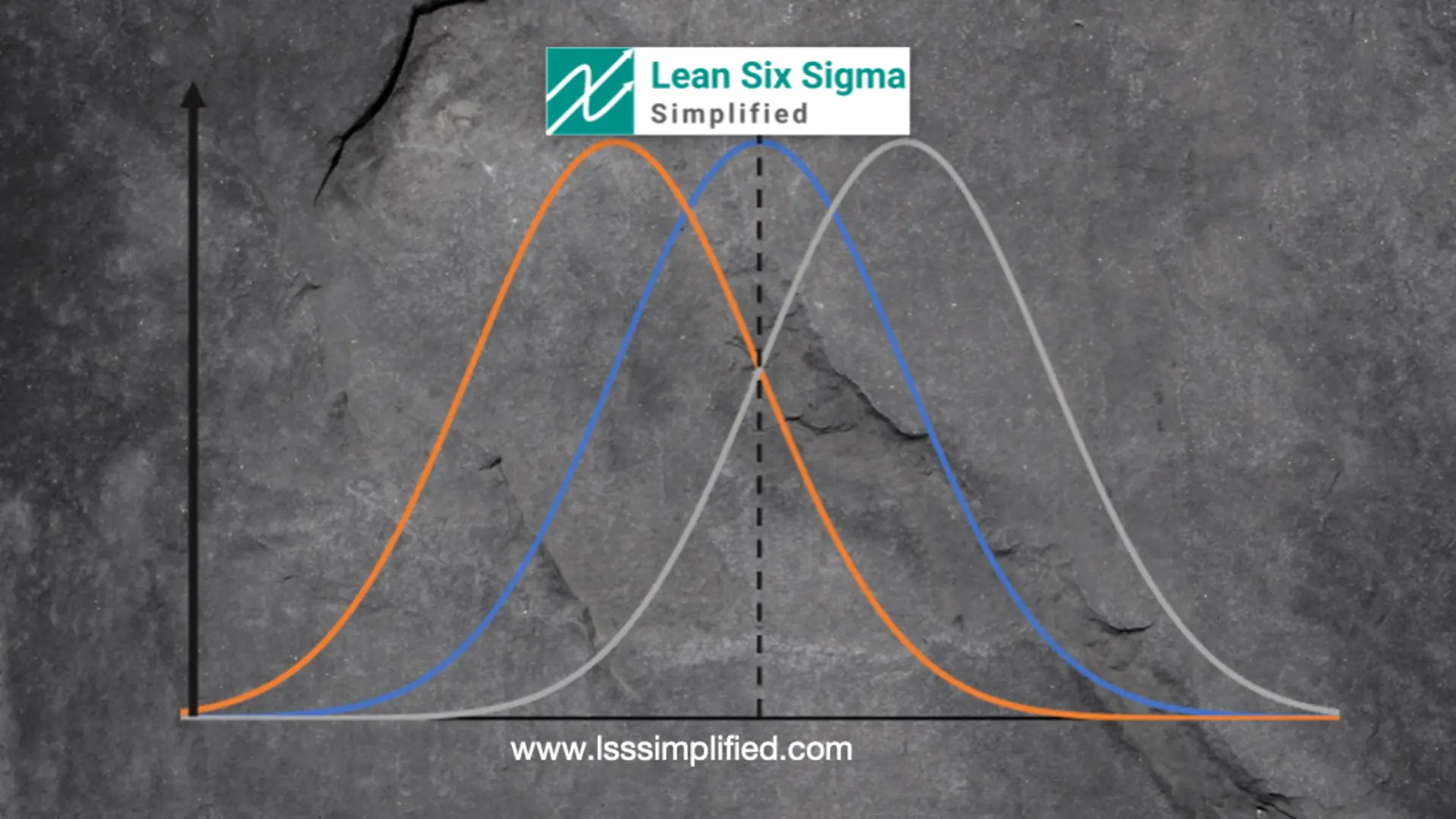
Normal Distribution for Lean Six Sigma

Probability Distribution for Lean Six Sigma
